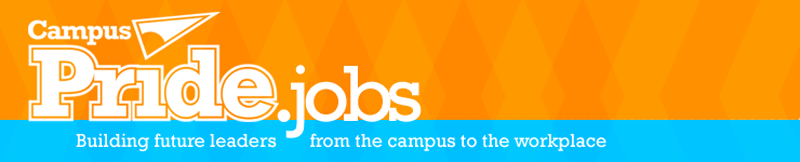
Job Information
Tyson Foods, Inc. Continuous Improvement Plant Lead - Zeeland, MI in Zeeland, Michigan
Certain roles at Tyson require background checks. If you are offered a position that requires a background check you will be provided additional documentation to complete once an offer has been extended. Job Details: Position: Continuous Improvement Plant Lead Reporting to: Plant Manager Working hours: Monday through Friday 7am or 8am to 5pm (weekends as needed- once a quarter) To feed a changing world, it takes an incredible team. From the cutting board to the board room, every Tyson Foods team member plays an important role in our success. That's where you come in. We are hiring immediately for a Continuous Improvement Plant Lead role. Setting the table for your success: At Tyson Foods, our team members' health and wellness is very important to us. We believe in helping our team members thrive inside and outside of the workplace. That's why we're committed to providing a holistic benefits package that provides support for you and your family. We invest in our team members and their success by providing resources like BENEFITS ON DAY ONE OF EMPLOYMENT and FREE EDUCATION! Benefits include: medical/Rx, dental, and vision coverage; 3 weeks paid vacation upon hire; 401(k) with employer match; stock purchase program; and product purchase program. We also offer CAREER GROWTH and much more! The plant Lean Leader is responsible for driving the Tyson Lean MOS (Manufacturing Operating System) processes and ensuring the plant is following the standardized methodology. This person will deliver lean training for any program changes and ensure that the site is up to date with any program governances changes. They will provide direction, teaching, and coaching to Team Members throughout the facility on the Tyson Lean MOS program. This individual will be responsible for advising the Plant Manager on how the team is doing with the processes and if the culture is owning the change. The Lean Leader will ensure the plant is maintaining the War Room, publishing the weekly report out, and developing the strategy with the team on how to mature the process to pass the next checkpoint. Responsibilities include: * Maintain all governance and program administration requirements for the plant. * Attend DMS Level meetings daily and provide teaching, coaching, feedback, and complete health checks. * Ensure problem solving methodology is being followed with weekly meetings, A3 documentation, backlog of projects, value of solutions, etc. * Publish weekly report out to leadership on lean journey and milestones achieved. * Maintain the War Room in conjunction with the standardized SOP and update all documentation on a weekly basis. * Maintain the action item registry and ensure visibility to site leadership as well as relevant stakeholders. This will include publishing the number of action items opened each week, closed actions, current open actions, and delinquent action items. * Be the liaison between the Corporate Lean Team which will provide direction on the program and processes and the Plant Manager for how ownership of the process is going at the plant. * Assess culture of adoption with the plant team by using the maturity assessment tool to define ownership. * Lean Leader is responsible to develop action plans with plant leadership to improve their processes to be eligible for the next set of lean tools within 90 to 120 days post-deployment. * Assist Operations Leadership with maintaining and updating all standard work instructions to align with the company standard. * Troubleshoot and escalate any issues related to the automated SPQDC boards. * Work in conjunction with Plant Manager to escalate any problems not remediated through problem solving processes to Level 4. * Ensure all documentation is done correctly and submitted along with the escalation. * Participate/Lead Kaizen events that get generated from problem solving escalations. * Collaborate with all cross-functional departments as needed to drive continuous improvement initiatives. * Comm