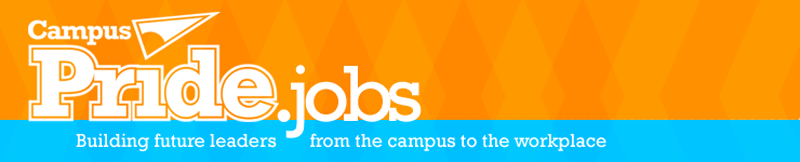
Job Information
Johns Manville Corp - Berkshire Hathaway Production Attendant in Waterville, Ohio
Production Attendant Waterville Plt 1 OH R24_2238 Full time
Who We Are
Johns Manville is a leading manufacturer and marketer of premium-quality insulation and commercial roofing, along with glass fibers and nonwovens for commercial, industrial and residential applications. Our products are used in a wide variety of industries including building products, aerospace, automotive and transportation, filtration, commercial interiors, waterproofing and wind energy.
A proud member of the Berkshire Hathaway family of companies, we serve customers in more than 80 countries around the globe. We are committed to delivering positive and powerful experiences, because we are successful only when our employees and customers thrive. We are passionate, we care about people, we perform at a superior level, and we protect others and our environments.
Compensation
The base hourly rate for this position is $20.01.
HOW IT'S DONE
Monitor filling of bulk chop pak boxes/tubs/bags and associated scales while completing other tasks. Record the weight when full, use lift to quickly remove the full box/tub/bag and replace with new box/tub/bag. Tare the scales using controls to begin filling. Remove the rack and unfold the bag of the removed box/tub. Inspect the cut of the fibers and notify supervisor of irregular cuts or quality. Close and secure the bag. Place lid on box and band shut. Label box/tub/bag accordingly. Transfer the serial number on the label onto the Production Sheet. Transport box/tub/bag to staging area using lift. Keep extra boxes/tubs/bags nearby in order to ensure timely removal and replacement of full ones.
*When on the Winder Level, monitor filling of boxes and remove when full and automatically shut off. Transport boxes/pallets on and off elevator as needed.
Monitor filling of 50lb bags or boxes while completing other tasks. Tape bag/box closed. Remove bags from boxes using lift assist. Place required number of bags in bulk boxes. Close, secure, and label boxes accordingly. Transport boxes to staging area using pallet lift. Keep extra boxes nearby in order to ensure timely removal and replacement of full ones. Verify filled box/bag weight by manually weighing and recording weight once per hour. Make needed adjustments to bring weight within spec. Notify supervisor as needed.
Use Package Specification number to gather supplies to stay ahead of production as needed. Supplies include pallets, tubs, boxes, bags, lids, etc. Notify Warehouse as needed to bring items to staging area. Assemble proper bulk and 50lb boxes and bags required for specific product. Keep extra boxes on hand.
Transfer required information from Production Sheet into the computer. Enter the work order number, machine number, UPC number, leg number, CPO number, PA number, and the weight of the product. Print out labels and label boxes/tubs/bags accordingly. Record shift, serial number, and dry weight onto the Direct Melt Production Sheet for each product.
Operate electric pallet truck to transport product released from hold area by Quality Control to staging area.
Use Production Sheet to determine how many boxes will be required on the Winder Level. Assemble boxes, place on pallets, and setup required bags in the boxes. Use Oscar/pallet lift to transport pallets to elevator and hook tool to drag pallets onto elevator. Maneuver pallets as needed. Secure doors and send down