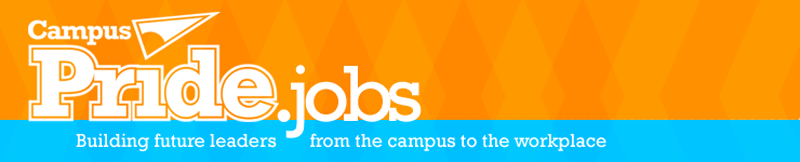
Job Information
Carhartt, Inc. Master Mechanic in United States
Location: US Supply Chain-TN or KY
Reports to: Director Process Engineering
Department: Manufacturing
Remote Status: On-site
FLSA: Exempt
Job Band: Professional
Job Summary
The Master Mechanic will provide best in class technical support in the identification, testing, training, and successful implementation of new equipment or processes in US manufacturing facilities. The position will also provide technical support in the troubleshooting and resolution of equipment or process issues that impact delivering expected outcomes in manufacturing.
Ways of the Carhartt Leader In our words and by our actions, we strive to emulate the hardworking example set forth by our founder, Hamilton Carhartt. We Lead Business by creating value, delivering on results, and making changes along the way. We Lead Self by being inclusive, recognizing that our differences make us stronger as we strive to build a better world, together, for all hardworking people. We Lead Others by communicating and clearly defining the path as we walk bravely into the future. Working at Carhartt, we are all given a seat at the table and the honor of continuing the legacy. Representative Responsibilities
Support and execute all facets of training for Supply Chain Mechanics at all US locations. Including but not limited to, identifying training, onsite training and conducting seminars as needed.
Provide training support to facility mechanics on new equipment or processes through the development of training manuals, providing onsite and remote support, etc.
Support US factories to deliver required services to support Made In USA business units. These services are not limited to but include embroidery, screen print, embellishment, etc.
Provide onsite and remote support to mechanics to resolve issues that are impacting delivery of quality or production expectations.
Work to develop equipment and/or attachments for specific operations or processes
Partner with Engineering/Mechanics to identify the proper equipment to support new product or services requirements
Develops test protocols and manages trials for new equipment. Support factory in the successful implementation of new manufacturing services offered in the US facilities.
Identify innovative cost savings ideas to improve methods, improve products, reduce indirect labor, improve processes, improve quality improvement, etc. on new and existing manufacturing processes.
Seeks out opportunities to design, develop, and implement equipment and technology related improvements to improve flexibility and response time
Remains aware and knowledgeable of the latest advances in equipment to support US manufacturing delivering requested services – for example washer, dryer, finishing, screen printing, embroidery, etc.
Required Education
Bachelors/Associates and/or Technical degree in Industrial or Mechanical/Electronic Engineering preferred or similar field of study or equivalent work experience.
Required Skills & Experience
Minimum of 10 years’ experience as a mechanic preferred (cutting, sewing, laundry and finishing processes).
Minimum of 5 years’ experience with Computer Numerical Controlled (CNC) equipment and Programmable Logic Controllers (PLC) preferred.
Knowledge of electricity, electronics, hydraulics, pneumatics, sensors, PLC, and automation .
Knowledge of Excel, Word, Outlook, CAM, CAD preferred.
Experience with safe use of machine shop equipment to include acetylene welders, arc welders, drill press and lathe, etc.
Ability to envision and drive innovative solutions for the Made in USA business unit.
Excellent verbal and written communication skills.
Proficient in organizational skills.