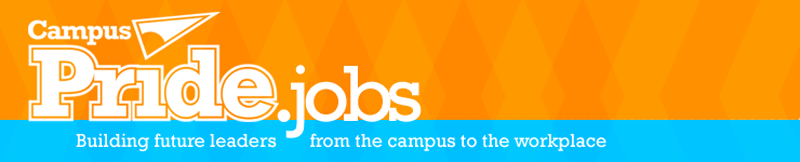
Job Information
United Alloy, Inc. Maintenance Manager in Vandalia, Ohio
United Alloy (UA) is the leading brand when to comes to metal fabrication and powder coating. UA produces the highest quality leak-proof metal fuel tanks, reservoirs, skids, frames, chassis, trailers, heavy metal fabrications, and complex weldments. At UA, our culture produces actively engaged people with sustainable results: safety, quality, productivity, and profitability. Each employee acts with a sense of ownership, takes initiative to problem solve, and is committed to the company’s mission, their team, and themselves.
In addition to our ISO 9001 certification, UA has been recognized as a WBENC woman/minority owned business. While we’re proud of these distinctions, one credentials stand above all others: our extensive list of long-term satisfied Fortune 500 OEM customers.
Be a part of an exciting growth initiative as we expand our operations with the opening of a new, state-of-the-art facility in Vandalia, OH. This is your chance to play a pivotal role in shaping the future of our organization and building a strong foundation for success.
Benefits: In addition to excellent starting wages, we offer a competitive compensation and benefits package as well as numerous perks.
Medical, Dental, Vision insurance
10 Paid Holidays
Responsible Time Off (RTO)
401(k) with company match
Bereavement Leave, Jury Duty, Military Leave and FMLA
Life Insurance, STD, LTD, Accidental Death & Dismemberment Insurance, Flexible Spending Account (FSA), and Dependent Care Account
Tuition Reimbursement
Key Employee Incentive Program (KEIP)
Referral Bonus
SUMMARY
The Maintenance Manager will exercise direct supervision over maintenance personnel, involving in the installation, maintenance, and repair of machines, tools and equipment, electrical systems, heating/cooling systems, facilities, structures, or equivalent.
ESSENTIAL DUTIES & RESPONSIBILITIES
Plan and assign work activities for maintenance staff to ensure optimal equipment performance and safety.
Monitor work areas and equipment to identify and address safety risks, maintenance needs, or violations.
Develop and oversee preventative maintenance schedules to minimize downtime and enhance efficiency.
Manage relationships with vendors and contractors to coordinate repairs, quotes, and cost controls.
Troubleshoot and resolve issues related to electrical, hydraulic, pneumatic, and CNC equipment.
Ensure building and grounds are maintained, including HVAC systems and general repairs.
Conduct and arrange training on safety and equipment use for team members.
Track maintenance budgets, expenses, and capital requirements, ensuring financial alignment.
Supervise and mentor maintenance personnel, fostering skill development and growth.
Support production by providing rapid troubleshooting and problem resolution.
QUALIFICATIONS
High school diploma or GED required; 5–10 years of supervisory experience in industrial maintenance.
Experience with laser, press, overhead crane, or forklift maintenance preferred.
Working knowledge of OSHA regulations, electrical theory, and safety protocols.
Familiarity with metal fabrication equipment and processes.
Strong troubleshooting, planning, and communication skills.
Ability to manage and prioritize tasks in a fast-paced environment.
Must comply with UAI and ISO standards and maintain a safety-first approach.
Ability to lift/move up to 50 pounds regularly and occasionally up to 100 pounds with assistance.
Demonstrates United Alloy’s 12 Expected Behaviors: 100% Responsible, Trustworthy, Team Player, Clear Communicator, Empathy, Humility, Emotional Self-Control, Resolves Conflict Directly, Positive Attitude, Respects Others, Problem Solver, and Agile.