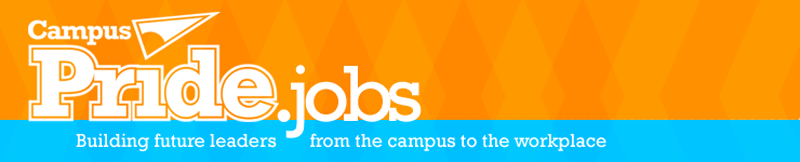
Job Information
TE Connectivity SR QLTY & RELIABILITY ENGINEER in Swindon, United Kingdom
SR QLTY & RELIABILITY ENGINEER
At TE, you will unleash your potential working with people from diverse backgrounds and industries to create a safer, sustainable and more connected world.
Job Overview
TE Connectivity’s Quality and Reliability Engineering Teams analyze the ability of product and production systems to comply with customer and contractual requirements through established reliability factors. They design, recommend revisions and install quality control systems, develop and document analytical methods for establishing reliability of products and their components and conduct analysis on relative reliability with regards to cost, structure, weight, maintainability, facility of production, and availability of materials and equipment. Out teams develop, implement and monitor company environmental safety programs and policies to ensure compliance with federal, state, and local environmental, health and safety regulations and recommend corrective actions if necessary. They are responsible for policies and practices to comply with applicable government regulations and industry requirements related to product environmental compliance, the implementation and management of technical and testing standards and specifications, quality control and reliability programs governing materials, product and processes, resulting in the optimization of material and labor, as well as failure analysis, root cause, corrective action and customer communication.
What your background should look like:
Role Statement:
The QMS Quality Engineer shall take the lead and oversee all aspects of the AD&M quality system, ensuring regulatory compliance is met. Working with critical processes and functions within the AD&M sites whilst focusing on continuous improvement initiatives to drive business excellence and zero-defect culture.You will be liaising with auditing organisations, notify bodies and regulatory authorities where necessary, in addition to supporting and carrying out the internal audit process within AD&M business unit As part of the role, you shall be responsible for rolling out global procedures, carrying out training along with implementing procedures where gaps are identified and report performance measures for quality improvements and compliance as well as providing knowledge and support to the company to enable operation of manufacture within regulatory guidelines and procedures.
Key tasks of the job:
• Representative for the quality management system
• Ensure awareness of compliance to regulatory certifications, TE Global QMS / 1AD&M and Customer requirements
• Manage all 3rd party audits and certifications including follow-up to closure of all related observations, improvements, major and minor non-conformance corrective and preventive action.
• Managing the internal audit programme ensuring effective close out of any Non Conformances and Opportunities for Improvement.
• Support the roll out of global procedures to enable standardisation of process and standards across TE AD&M
• Collating and reviewing the quality management system and compliance documentation
• Support with the maintenance of procedures and work instructions for processes ensuring that the agreed practice is reflected accurately in the Quality Management System
• Promote a high standard of awareness and understanding at site level of all appropriate policies, procedures with Implementation of training programmes associated to quality management system awareness. i.e. new start inductions.
• Regularly report on quality metrics within the organisation to management
• Identify gaps and act as a proactive partner in driving change and developing solutions in close collaboration with site continuous improvement team. Drive of COPQ. MRB, Customer Complaints.
• Conduct quality assurance reviews with operational business management / supply chain management to review ongoing action planning for improvement.
• Engage with sites on TECHs (TE Complaint Handling Systems) 8D management, reporting associated KPI requirements in line with business needs and associated administrative tasks.
• Deliver quality assurance training as and when requested
Qualifications and Experience required:
• Experience in working in an engineering manufacturing environment
• Significant experience in a Quality Management Role
• Good knowledge of change control
• Experience working and developing strong relationships with customers and suppliers.
• Proven six sigma and lean experience
• Strong knowledge of ISO9001 / AS9100 & IATF16949
• Strong knowledge and practical experience of quality tools including but not limited to 8D, FMEA, 5Y, FAI’s, PPAP & APQP
• Experience in complying with customer, statutory and regulatory requirements in a manufacturing environment.
• Travelling: 50 % EMEA region mostly
Competencies required:
• Managing and measuring work
• Motivating others
• Building effective teams
• Values: Integrity, Accountability, Teamwork, Innovation.
• SET: Strategy, Execution, Talent
Competencies
Values: Integrity, Accountability, Inclusion, Innovation, Teamwork
Location:
Swindon, SWD, GB, SN1
City: Swindon
State: SWD
Country/Region: GB
Travel: 50% to 75%
Requisition ID: 122243
Alternative Locations:
Function: Engineering & Technology
TE Connectivity and its subsidiaries, affiliates, and operating units (collectively, the "Company") is committed to providing a work environment that prohibits discrimination on the basis of age, color, disability, ethnicity, marital status, national origin, race, religion, gender, gender identity, sexual orientation, protected veteran status, disability or any other characteristics protected by applicable law or regulation.