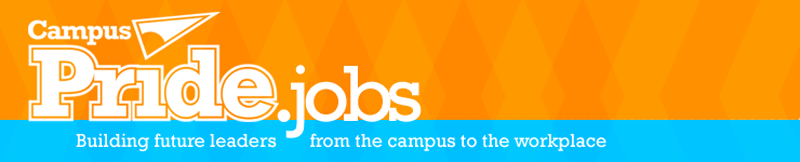
Job Information
Scot Forge Company Segment Quality Engineer in Spring Grove, Illinois
Segment Quality Engineer
Position Summary:
Segment Quality Engineer will provide leadership on industry specific quality systems requirements, primarily aerospace and defense industries. For the assigned industry, he/she will ensure our business processes and systems meet the expectations for compliance, responsiveness, and integrity. This role will serve as the segment’s lead quality resource supporting sales, process engineering, and the shop as it relates to interpreting customer/industry specifications, ensuring individual order compliance, aligning functional procedures for compliance, and coordinating internal resources for implementing process improvements to ensure segment quality expectations. The individual in this role must have the problem solving and facilitation skills to challenge and strengthen processes while demonstrating collaboration skills required to pull resources together and provide sustainable processes.
Required Qualifications:
Must be a U.S. citizen or hold a current Permanent Resident Card
BS in engineering or metallurgy or equivalent
Minimum 5 years of experience as a quality resource in a high specification environment (Military, Nuclear, Aerospace, FDA, ETC)
Experience in reading & interpreting specifications and technical documents
Significant experience in Structured Problem Solving (8D, A3 or other)
Good written and oral communication skills
Preferred Qualifications:
Experience in heavy manufacturing environment
Good understanding of lean/sigma tools
Previous experience in the metals industry and/or metallurgy knowledge.
Excellent Project Management Skills
Qualified Lead auditor in systems such as ISO 9001:2008, AS9100.
Essential Job Duties and Responsibilities
Coordinate segment specific QMS activities with customers and governing bodies regarding our quality system. Coordinate change management of quality system activities, assuring the system meet requirements.
Must read and interpret complex specifications and contracts from multiple industries including but not limited to: Military, Nuclear, Aerospace, and Oil and Gas. This role will serve as a key authority resource for the interpretation of specifications and be willing to provide written and verbal guidance to regulators, customers, and industry groups.
Assures company compliance to the industry/customer specifications by facilitation of requirements compliance. Using project management skills, to work with internal process owners developing implementation project plans ensuring effective implementation of the process requirements. Examples include NADCAP, AMS process requirements.
Integrating into the order development; this individual will review industry and customer specifications/contracts and, working with quality assurance specialists, process engineers, and sales, will ensure new order packages communicate all compliance requirements.
Support Scot Forge auditing program by performing duties of lead auditor for both internal and external supplier audits.
Represent Scot Forge in communication with customers’ sales, quality and technical resources regarding specification/contract requirements, manufacturing and process capabilities, and questions / complaints related to quality systems, product, processes, or documentation.
Support sales and process engineering in the creation, communication, and resolution of segment specific quality issues including NCRS and deviations.
Lead/work with a cross functional team to identify root cause and develop and implement positive corrective action(s) to correct identified problem(s). Use, train, facilitate and coach teams in the proper use of Structured Problem-Solving tools. Drive CAR’s to completion.
Communicate and provide training regarding execution of procedures and interpretation of specifications/drawings as they apply to the technical manufacturing, test and inspection requirements invoked by customers.
Utilize metrics to evaluate and eliminate waste for implemented processes. Support and participate 6’s / Lean activities.
Provide plant floor level quality culture leadership enabling the teams to fully understand their quality impact on our customers, our employee owned business, and their individual work groups.
Train, support, and audit assigned areas ensuring education and compliance to all appropriate customer and industry requirements
Working Conditions/Physical Requirements:
Primarily working in office environment, with exposure to manufacturing floor
Role flexibility is a requirement for all employee owners which may include cross training in the following areas/roles:
Quality Engineer – Shop
Quality Assurance Specialist
Process Engineering
We are proud to be an Equal Employment Opportunity employer: M/F/Disabled/Vets encouraged to apply.
We maintain a drug-free workplace and perform pre-employment substance abuse testing