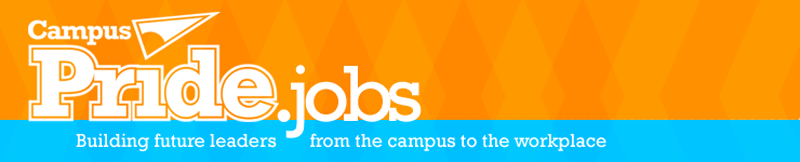
Job Information
Scot Forge Company Quality Assurance Specialist in Spring Grove, Illinois
Scot Forge Company is seeking a Quality Assurance Specialist to support our owners by providing Compliance expertise to our complex customer markets (Commercial Nuclear, Naval Nuclear, Aerospace, and Military). This role will primarily focus on working with Sales, Process Engineering, Manufacturing Engineering, and Production Departments to ensure that customer requirements are met. Responsibilities include:
Navigate, read, and interpret specifications as they apply to the appropriate industry
Review and prepare product documentation / certification packages to ensure data accuracy
Support production by accurate and timely review of certifications
Meet quality and productivity targets that have been established by the department supervisor
Represent Scot Forge as we effectively communicate with customers and 3rd party auditors regarding specification requirements, manufacturing and process capabilities, and questions / complaints related to quality systems, product, processes, or documentation
Roll out customer and industry requirements by communicating and providing training to personnel regarding execution of procedures and interpretation of specifications / drawings as they apply to the technical manufacturing, test, and inspection requirements invoked by customers
Support second- and third-party external audits and customer witnesses and their review of Scot Forge Quality System processes
Ability to lead and / or work with a cross-functional team to identify root cause and develop and implement positive corrective action(s)
Drive for continual improvement Company-wide for customer certifications
Establish, implement, and maintain procedures and best practices that will drive for error-free certifications
Actively participate in applicable safety programs (SafeStart, Target Zero, etc.) to ensure the continued success of the program
Maintain knowledge of process through training, perform scheduled observations, and provide quality feedback
Work in cooperation with all fellow employees
Utilize metrics to evaluate and eliminate waste for implemented processes
Support SF auditing program by performing duties of lead auditor
Administer, participate, and support the LPA (Layered Process Audit) system
Create certification per Shop Order Requirements
Correct certifications as required
Create and distribute standardized quality reports such as NCR reports, calibration reports
Create deviation requests per internal procedures
Qualifications:
Associates Degree in Industrial Technology
Minimum three years’ experience in reviewing certifications to industry and customer specifications
Familiar with the MS Office Suite of Applications
Proficient in typing and highly accurate in transcribing information
Auditing experience – ISO9001, AS9100, NQA-1, ISO17025, ASME Y14.5, ASME Section III
Familiar with reading blueprints / complex drawings
Familiar with destructive and nondestructive testing
Basic understanding of Structured Problem Solving (8D)