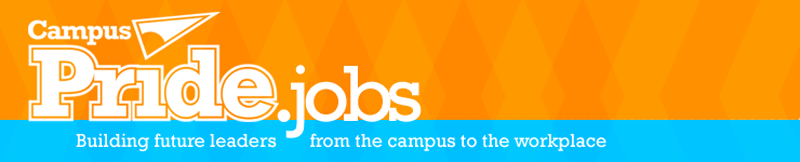
Job Information
Clearwater Paper Corporation Sr Process Engineer - Manufacturing Technical in Spokane, Washington
Description Clearwater Paper (NYSE: CLW) is a publicly held company and a premier supplier of private brand tissue to major retailers, including grocery, drug, mass merchants and discount stores. In addition, the company produces bleached paperboard used by quality-conscious printers and packaging converters, and offers services that include custom sheeting, slitting, and cutting. Clearwater Paper's employees build shareholder value by developing strong relationships through quality and service. Working at Clearwater Paper provides an opportunity to enrich your career through challenging and meaningful work and ongoing training and development-all in a supportive environment. We know our success depends on your success. What you will do: The Manufacturing Technical Engineer will serve as a leader in the development and continuous improvement effort of the manufacturing process. Key focus areas include safety, quality, cost, yield, waste, manufacturing uptime, process improvement, and process reliability. The successful candidate will act as a technical resource for the corporate technical team supporting and leading projects and process improvement efforts in the papermaking and converting operations. Technical Assistance Evaluate new technologies, implement process changes, and develop systems to reduce operating costs, increase production, and improve quality. Leads data analysis, loss analysis, and technical troubleshooting efforts. Provides support data, data analysis, and technical recommendations for troubleshooting efforts, technical reports, and performance updates. Utilizes Data analysis to reduce variability or improve performance. Assists with designing solutions to eliminate equipment failures and process instabilities. Writes procedures, trains operators, and monitors compliance with quality procedures. Travels to mill sites to engage with production operations teams and for troubleshooting efforts and improvement projects. Process Improvement Develops working knowledge of all process areas in areas including process flow, operator responsibility, major quality attributes, and areas for improvement. Initiates, conducts and documents results of process trials to improve productivity and/or quality. Assists with proposals to justify capital expenditures, help manage technical aspects, and assist with coordination of start-up of capital projects. Recommends and implements process improvements or chemical changes to improve the overall operation where applicable. Optimizes process by identifying and eliminating root causes of process variations. Assists with data collection and data analysis for justification of capital expenditures and coordination of start-ups. Conducts crew training in new process equipment or chemical additives. Monitors process variables and recommends changes in operation for improved performance. Monitors performance of wearable items (clothing, coater blades, doctor blades, etc.) and recommends changes leading to cost reduction, quality enhancements, or production improvement. Leadership Participates in the development of less experienced engineers. Provides crew supervision during trials or upset conditions, or troubleshooting efforts to ensure the trial plans or troubleshooting efforts are properly executed. Mentors operations employees to ensure good technical and troubleshooting skills. Collaborates with other areas internal and external to the site and the corporation. Track, communicate, and share in accountability of profit/cost improvement tracking. Key Competencies and Attributes Actively seeks and allocates appropriate decision-making authority or task responsibility to appropriate individuals based on their abilities, availability, motivation, and development needs; considers potential positive and negative impact, business unit priorities, organ