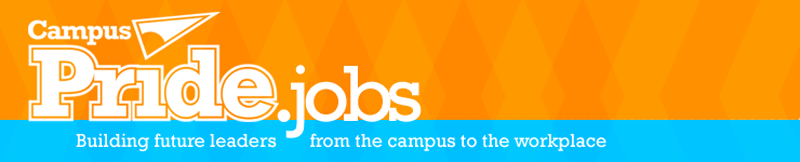
Job Information
Blue Origin LLC New Shepard Supervisor 2nd shift (R37287) in Seattle, Washington
At Blue Origin, we envision millions of people living and working in space for the benefit of Earth. We're working to develop reusable, safe, and low-cost space vehicles and systems within a culture of safety, collaboration, and inclusion. Join our diverse team of problem solvers as we add new chapters to the history of spaceflight! This role is part of Blue Origin Operations, which is comprised of Integrated Supply Chain, Facilities, and Security. This includes Manufacturing and Supply Chain support across all Blue Origin facilities. As part of a hardworking team of diverse specialists, technicians, and engineers, you will Supervise the production operations team overseeing all functions of planning, scheduling, demands, assembly, and operations. Implements strategies meant to improve the organization's financial performance and competitive positioning through continuous improvement of production-related processes. Identifies manufacturing processes or procedures that could benefit from process improvement or efficiency optimization, and approves the implementation of changes. As part of a small, passionate, and accomplished team of experts, you should have an excellent technical understanding of complex assemblies and production environments building human-rated vehicles. This role will involve the management of technicians and specialists on the production floor specializing in sub-orbital human and payload launch vehicles supporting the New Shepard program. Special Mentions Relocation provided Travel expected up to 0-25% of the time as needed Shifts available: B-Shift 4 10 hour days Swing shift Interviews will include a technical assessment Responsibilities include but are not limited to: Coordinate and steer the collective efforts of Crew Capsule integration and production technicians. Enforce area standards and operational rules (includes annual reviews, regular mentoring, and disciplinary action). Interface with area leadership from around the factory and prioritize work based on production schedule and organizational goals. Schedule risk identification and mitigation. Coordinate support organization efforts to minimize production interruptions. Ensure product quality and conformance to specifications. Improve area safety and efficiency through regular auditing and continuous improvement. Establish and analyze area metrics for trend extrapolation to drive the following: Personnel training and development. Development and implementation of efficiency improvement projects. Optimization of product flow through the factory. Root cause analysis and the implementation of corresponding corrective action plans. Identification and elimination of defects within the area value stream. Reduction of downtime for product and personnel. Lead efforts to transition product from engineering development to full-rate production. Review drawings and technical data packages for manufacturability, and provide constructive feedback to the engineering/design community. Participate in and lead daily production standup meetings as well as facilitate seamless transition between shifts. Operate on an off-shift (Evenings) managing day to day activities with minimal oversight and support. Minimum Qualifications: 5 years experience in aerospace vehicle manufacturing environment. Minimum of 3 years in a leadership position leading a team of 15+ people. Lean manufacturing training and experience. Experience monitoring, tracking and continually improving total cost equation. Experience with applying lean manufacturing principles, and efficiency methods required. Demonstrated ability to read and interpret controlled documentation and processes such as mechanical drawings, GD&T, assembly procedures/work instructions, schematics, engineering drawings, and parts lists. Must be able to set a high