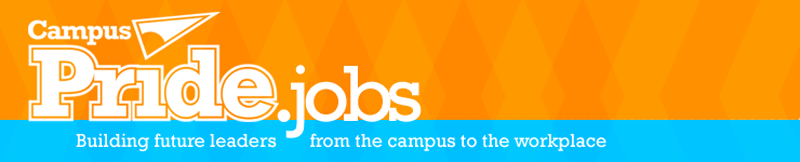
Job Information
J&J Family of Companies Principal Product Development Engineer in Santa Clara, California
Johnson and Johnson Med Tech is recruiting for a Principal Product Development Engineer, Supply Chain Engineering in Santa Clara, CA!
At Johnson & Johnson, we believe health is everything. Our strength in healthcare innovation empowers us to build a world where complex diseases are prevented, treated, and cured, where treatments are smarter and less invasive, and solutions are personal. Through our expertise in Innovative Medicine and MedTech, we are uniquely positioned to innovate across the full spectrum of healthcare solutions today to deliver the breakthroughs of tomorrow, and profoundly impact health for humanity. Learn more at https://www.jnj.com/. Are you interested in joining a diverse team that is helping improve patient care and drive innovation? Apply today!
Job Summary/Overview:
Our team of engineers, designers, and technical specialists are in the forefront of technology in the medical device industry. As the Principal Development Engineer, you will make vital contributions to the New Product Development (NPD) and NPI (New Product Introduction) pipeline and transform patient care through innovation. Our Development Engineering staff works with NPD teams and Suppliers to develop robust component designs and manufacturing processes that meet or exceed all Product requirements.
The Principal Product Development Engineer is a key team member product pipeline will work closely with multi-disciplinary engineering teams to develop sophisticated medical devices. Candidates must be self-motivated, independent and have an eagerness to learn and work as a team, and a desire to thrive in a dynamic environment. In this position, you are expected to demonstrate sophisticated electrical and mechanical engineering knowledge, be able to independently resolve approaches to difficult technical problems and communicate broadly across engineering teams and associated management.
Duties & Responsibilities:
Collaborate with internal and external partners to plan, design, develop, qualify, and stabilize component and equipment processes for New Product Development (NPD) projects.
Lead discussions among R&D, Manufacturing, and Suppliers to implement robust manufacturing processes, integrating Design for Manufacturing (DFM), Design for Assembly (DFA), and Design to Cost (DTC) principles.
Serve as a liaison between R&D, Product Management, Quality Assurance, and suppliers, ensuring that the "voice of manufacturing" influences product design.
Support Design Transfer activities to facilitate a smooth transition of new products into manufacturing.
Utilize engineering principles and advanced manufacturing techniques, alongside statistical analysis, to address complex technical challenges and establish new methods and standards.
Drive continuous improvement initiatives and foster effective communication across teams and stakeholders.
Design and execute assembly line process characterization, PFMEAs, and control strategies, ensuring compliance with Good Manufacturing Practices (GMP).
Oversee engineering builds and pilot production runs, conducting root cause analyses of assembly failures.
Manage project deliverables and track component design changes to minimize impacts on assembly processes.
Qualifications
Qualifications:
Required:
Minimum B.S. (Mechanical, Electrical, or other related Engineering field or equivalent) and 10 years of industry experience.
Engineering experience in either mechanical, electrical, or electro-mechanical products and components or equipment.
Experience in Design for Manufacturing or Assembly (DFM/A) around injection molding, machining, and optical equipment.
Experience working closely with external or third-party suppliers.
Knowledge and demonstrated application of regulated medical device development processes, standards, and guidelines, including but not limited to 21 CFR 820, ISO 13485, ISO 14971, and IEC 60601.
Measurement Systems Analysis experience (e.g., GR&R).
Statistical Analysis knowledge (e.g., Design of Experiments (DOE), Process Stability/Control/Capability) and PFMEA.
Understand equipment concept creation, review approval, build, runoff, FAT, software validation, IQ, OQ, and PQ road map requirements.
Proven interpersonal and communication skills, with the ability to work successfully in a team environment.
Strong technical communication skills and proven ability to work independently.
Solid understanding of regulatory requirements regarding the design, build, and release of medical devices, worldwide, preferred.
Up to 30% domestic and international travel required.
Preferred:
Advanced Degree.
Experience designing, developing, and testing the manufacturing of electromechanical, fiber, or laser equipment and systems, including test and process development.
Knowledgeable about medical-specific assembly technologies, the equipment supplier base, and the capabilities of the suppliers.
Process Excellence Six Sigma knowledge or certification.
Test methods development (TMD) & Test methods validation (TMV) experience.
Experience with one or more of the following: laser welding, riveting, laser etching, soldering, pressing, joining, extrusion, over molding, coating, and/or design for assembly experiences.
The anticipated base pay range for this position is 113000 to 195500. California Bay Area - The anticipated base pay range for this position is 139000 to 224825.
The company maintains highly competitive, performance-based compensation programs. Under current guidelines, this position is eligible for an annual performance bonus in accordance with the terms of the applicable plan. The annual performance bonus is a cash bonus intended to provide an incentive to achieve annual targeted results by rewarding for individual and the corporation’s performance over a calendar/performance year. Bonuses are awarded at the Company’s discretion on an individual basis. · Please use the following language:
Employees and/or eligible dependents may be eligible to participate in the following Company sponsored employee benefit programs: medical, dental, vision, life insurance, short- and long-term disability, business accident insurance, and group legal insurance.
Employees may be eligible to participate in the Company’s consolidated retirement plan (pension) and savings plan (401(k)).
This position is eligible to participate in the Company’s long-term incentive program.
Employees are eligible for the following time off benefits: - Vacation – up to 120 hours per calendar year
Sick time - up to 40 hours per calendar year; for employees who reside in the State of Washington – up to 56 hours per calendar year
Holiday pay, including Floating Holidays – up to 13 days per calendar year of Work, Personal and Family Time - up to 40 hours per calendar year
Additional information can be found through the link below. https://www.careers.jnj.com/employee-benefits
The compensation and benefits information set forth in this posting applies to candidates hired in the United States. Candidates hired outside the United States will be eligible for compensation and benefits in accordance with their local market."
Johnson & Johnson is an Affirmative Action and Equal Opportunity Employer. All qualified applicants will receive consideration for employment without regard to race, color, religion, sex, sexual orientation, gender identity, age, national origin, or protected veteran status and will not be discriminated against on the basis of disability. We will ensure that individuals with disabilities are provided reasonable accommodation to participate in the job application or interview process, to perform essential job functions, and to receive other benefits and privileges of employment. Please contact us to request accommodation.