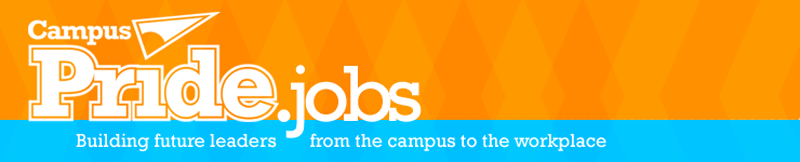
Job Information
LOC Performance Products, Inc Facilities Improvement Manager in Saint Marys, Ohio
Job Summary:
The Facility Improvement Manager is responsible for driving operational excellence and implementing continuous improvement strategies to enhance the efficiency, safety, and overall performance of the manufacturing facility. This role involves analyzing current processes, identifying opportunities for improvement, and collaborating with cross-functional teams to implement innovative solutions. This role offers the opportunity to make a significant impact on the facility’s operational efficiency and contribute to the organization’s long-term success.
Essential Functions:
Actively seek out and be aware of processes or improvements that could impact customer satisfaction, including delivery time and quality of products produced.
Organizes efforts to ensure that late deliveries are avoided.
Collaborates with production managers, value stream managers, and supervisors to support plant improvement.
Works closely with the operators and operations staff on value stream and departmental projects.
Engages the plant operators to support potential improvements and improve the training program.
Work actively with the Plant Manager to complete projects and continuous improvement activities.
Document all improvements though key performance indicators including, but not limited to efficiency improvements, and cost improvements.
Documents project success with visual aids, including before, during, and after completion of projects.
Works closely with the plant Safety team to ensure that plant safety objectives are met.
Works within the waste department with process engineers and supervisors to support gaps between waste objectives, and reductions plans.
Collaborates and supports at all levels as a mean to improve plantwide communications and implement best practices.
Manage budgets, timelines, and resources for facility improvement projects.
Seeks out improvements that would streamline supervisory responsibilities on the shop floor.
Creates a standard in training that is sustainable across all departments.
Works with the inventory and ERP Team (Plex) to support improved inventory discrepancies
Reports on alignment to the management staff.
Develop and maintain KPIs for effectiveness of the continuous support program at the facility.
Minimum Qualifications:
Knowledge, Skills and Abilities (as demonstrated through experience, training and/or testing)
Strong knowledge of Lean Manufacturing, Six Sigma, or similar methodologies.
Exceptional oral and written communication skills
Knowledge of industry trends, emerging technologies, and best practices in manufacturing operations.
Ability to lead by example, to support alignment and show consistency.
Excellent analytical, problem-solving, and decision-making skills.
Ability to lead cross-functional teams and manage multiple projects simultaneously.
Effective communication and leadership abilities to inspire and engage stakeholders at all levels.
Education:
- Bachelor's degree required in Engineering, Project Management, Business, Supply Chain, or a related field; or equivalent combination of education and experience.
Experience:
- 5+ years of experience in manufacturing operations, with a focus on process improvement and project management.
Background Prerequisites:
- Must undergo and meet company standards for background check, employment verification, reference checks and controlled substance testing.
Preferred Qualifications:
- Bachelor’s degree preferred in Engineering, Project Management, Business, Supply Chain, or a related field.
While performing the duties of this job, the employee is occasionally required to stand; walk; sit; use hands to finger, handle, or feel and reach with hands and arms. The employee may occasionally lift and/or move up to 50 pounds. Reasonable accommodations may be made to enable individuals with disabilities to perform the essential functions.
ARV is an Equal Employment Opportunity (EEO) employer. It is the policy of the Company to provide equal employment opportunities to all qualified applicants without regard to race, color, religion, sex, sexual orientation, gender identity, national origin, age, protected veteran or disabled status, or genetic information.
American Rheinmetall Vehicles, formerly known as Loc Performance Products, LLC provides full services for complex mechanical products, fabricated structures and systems that range from complete design services to prototype manufacturing, testing, production launch, full rate production and product service and sustainment. ARV provides quality products and services at affordable prices through a lean organizational structure . The Plymouth, MI facility serves as corporate headquarters and specializes in suspension, driveline, and track systems. The Lansing and Lapeer Michigan based facilities specialize in fabrications and armor product solutions. While our St Marys, OH facility serves both the DOD and Commercial lines.