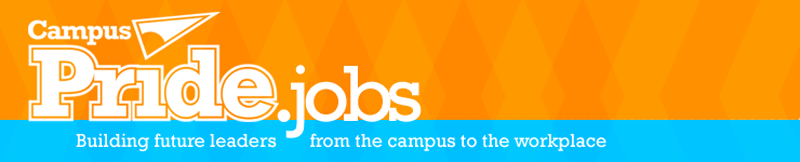
Job Information
Rivian Senior Manager, Material Flow Engineering in Plymouth, Michigan
About Rivian
Rivian is on a mission to keep the world adventurous forever. This goes for the emissions-free Electric Adventure Vehicles we build, and the curious, courageous souls we seek to attract.
As a company, we constantly challenge what's possible, never simply accepting what has always been done. We reframe old problems, seek new solutions and operate comfortably in areas that are unknown. Our backgrounds are diverse, but our team shares a love of the outdoors and a desire to protect it for future generations.
Role Summary
The Rivian Supply Chain team is looking for a highly motivated and accomplished Supply Chain Engineering professional to bring Rivian's engineered products to life. In this role, the Senior Manager will be responsible for leading a team of talented managers and engineers to develop a brownfield material flow optimization strategy for our manufacturing facility in Normal, IL and create a greenfield benchmark flow for our future location in Stanton Springs, GA. On our team, we expect our people to own every aspect of the engineering process, from concept design to successful implementation and everything in between. This role reports to the Director of Supply Chain Engineering and requires 50% travel to our facilities in Illinois and Georgia.
Responsibilities
Develop strategies to reduce the plant's Total Delivery Cost through the implementation of lean continuous flow principles and resourceful automation solutions
Develop a material flow "want to be condition" for the Normal facility.
Create a benchmark greenfield material flow for Stanton Springs, GA
Coordinate and help develop a progress-based pull system to synchronize all last mile and internal material flow processes.
Spearhead the development of world-class Jidoka kitting and sequencing systems, leveraging technologies such as PtL, Andon, CoBots, and karakuri.
Lead initiatives related to takt time adjustments and minor/major model launches for material handling.
Provide leadership, coaching, mentorship, and professional development to your team.
Implement training plans to improve overall organizational strength and capability.
Successfully execute projects within established schedules and annual expense/capital budgets.
Offer guidance in analyzing production issues, proposing effective countermeasures, and resolving material-flow related challenges.
Responsible for and ensure safety, quality, cost, timing & throughput targets are achieved on all projects.
Qualifications
10+ years of management experience in automotive or Tier 1 with an emphasis in Logistics, Transportation, Operations, Supply Chain or related field.
BS/BA in Logistics, Operation, Supply, or equivalent work experience.
Demonstrated track record of defining, launching, and driving major process redesign initiatives to enhance both internal and external material flow operations.
Proficiency in Lean, Six Sigma, or TPS (Toyota Production System) methodologies.
Intermediate to advanced knowledge in Excel, Word, Power point, and Outlook programs.
Strong analytical skills and ability to communicate effectively.
Ability to prioritize tasks and responsibilities.
Trained in 8-Step or similar problem-solving discipline.
Strong team orientation and cross functional attitude.
Ability to create and present summary reports.
Ability to speak effectively before groups of customers or employees of organization.
Ability to communicate in a high-pressure environment.
Pay Disclosure
Salary Range for California Based Applicants: $168,000 - $211,000 (actual compensation will be determi