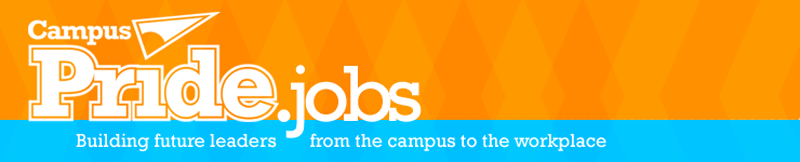
Job Information
Good Foods Group, LLC. Bilingual Production Supervisor (3rd Shift) in Pleasant Prarie, Wisconsin
Description
Job Summary:
As a key member of the production team, the Production Supervisor monitors and coordinates production team activities, giving importance to individual member's and overall team's achievement of established goals. This individual will be accountable for Safety, Quality, Delivery, Cost, and Inventory (SQDCI), as well as, holding responsibility for all Operations assigned on the shift and acting as liaison between Group Leaders and the rest of the organization.
Job Responsibilities:
• Lead Group Leaders to ensure a safe working environment, produce high quality products with timely results in a customer focused environment
• Understand and convey the goals, objectives and focus of the organization at the shift level
• Plan work, assign tasks, instruct, direct, and assist the team through the hour-by-hour charts
• Comprehensive knowledge of general food safety program best practices and must be highly proficient in ability to document and work within GMP’s, HACCP, HACQP and SQF
• Review and sign off documentation for company CCPs to ensure proper compliance to SQP policies
• Review work and make corrections as needed to ensure quality product and proper documentation
• Maintain discipline, morale, and harmonious personnel relations; address primary concerns
• Contribute to employee performance appraisals
• Develop and enhance the team's efficiency, execution capabilities and technical excellence to attain goals
• Provide strategic assistance to Group Leaders and Team Leaders in the areas such as schedule optimization, staffing development, and inventory management
• In collaboration with the Safety Manager, maintain and ensure the safety of all team members in operations through proper training, enforcement of safety rules, and following proper procedures
• Maintain a clean and safe working environment in compliance with all company policies as well as regulatory agency standards
• Understand and enforce all company policies and procedures as well as good manufacturing practices
• Improve departmental efficiencies so that downtime is minimized using the hour-by-hour boards, problem solving strategies, and collaboration with other departments/shifts
• Work closely with all levels of management in the areas of production, maintenance, Quality Assurance, logistics and sanitation
• Plan and initiate cross training of employees to expand job knowledge and add flexibility to scheduling the workforce
• Ensure proper planning and training of all team members within the allotted timeframe
• Ensure proper and accurate reporting of all daily requirements
• Notify Management of any repairs or adjustments that are required
• Effectively conduct production team meetings
• Show strong ability to effectively manage time to handle multiple priorities at once and close out tasks in a timely fashion
• Comply with all Company rules, regulations, and policies
• Perform other duties as assigned
Qualifications and Additional Skills:
• Must be 18 years of age or older
• GED or high school diploma is required
• Food Manufacturing experience is preferred
• Lean / Six Sigma Green Belt certification within 12-month span
• Bilingual (English – Spanish) preferred
• Ability to read, comprehend and follow complex written instructions
• Strong communication and written skills
• Must be able to interact well with other team members
• Must be a self-starter and able to work without close supervision
• Willingness and ability to work in a team environment
• Ability to understand different units of measure and record information
• Strong safety knowledge and safety record
• Walk for extended periods, stand, and reach with hands or arms
• Must have strong interpersonal skills such as: communication, organization, confidence, respect, fairness, integrity, influence, delegation, facilitator, negotiation, willingness, etc.
• Proficiency in MS Office Suite, Microsoft Dynamics, or related ERP
Travel:
• None Required
Work Environment:
• The employee is subject to production environment approximately 85 percent of the work time. (Wet environment with temperatures in the range of 38 to 40 degrees)
• Medium/High noise levels from operating machines
• Physical hazards from moving equipment and machine parts
• Frequently required to use personal protective equipment to enforce Good Food Manufacturing (GMP’s) processes.
Physical Requirements:
• Able to hold stationary positions for extended periods of time
• Able to communicate information accurately to others
• Able to detect and discern sounds accurately in order to exchange information
• Able to move throughout workspace frequently
• Adjust self to stooping, reaching, crouching, and twisting positions on occasion
• Able to observe details at close range, perceive colored images as well as effectively perceive computer generated images on a screen
• Inspect, activate, operate, and position any appropriate machinery functions
• Must be able to lift up to 40 pounds occasionally
• Able to work overtime and/or weekends
Direct Report(s):
• Laborer and Machine Operator(s)
Background Check:
• Level II
This job description is not intended, nor should it be construed to be an exhaustive list of all responsibilities, duties, skills, or working conditions associated with a particular job. It is intended only to be a general description of the essential functions common to positions of this type. Nothing in this job description restricts managements right to assign or reassign duties and responsibilities to this job at any time.