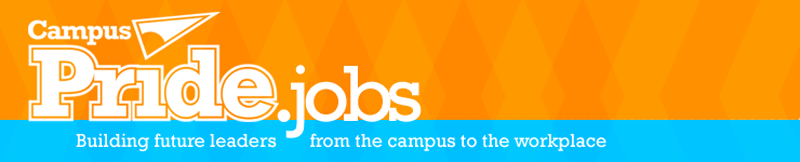
Job Information
Caban Systems Production Quality Manager in Plano, Texas
Production Quality Manager Plano, Texas
About Caban
Caban Systems, a leader in the design and manufacture of software-enabled energy storage and management systems for the telecommunications industry, delivers modern infrastructure solutions to its customers, while substantially reducing operational expenses and increasing uptime.
We deploy end-to-end turnkey solutions with a three-part system solution, including lithium-ion energy storage systems, cloud-based remote monitoring software, and Energy-as-a-Service (EaaS) offering for mobile sites, fixed networks and fiber nodes. Our energy management system is designed to supply primary and backup power for reliable connectivity, increased transparency and a significant reduction in emissions.
Job summary Responsibilities
Lead an effort to embed a process-driven, continuous improvement method into the business.
Deploy and train continuous improvement methodologies such as lean business and manufacturing methods, advanced problem-solving techniques, and approaches to visual workplace management.
Direct and support site Operational Excellence resources to drive continuous process improvement activities for cost reductions and improved quality.
Develop strong partnership with all Operations leadership to validate process activity and performance.
Facilitate and drive change in a fast paced and “ever changing” environment leveraging his/her strong interpersonal, professional, and collaborative skills.
Ensure projects are integrated and aligned with other business activities, improvement projects and business strategy and coordinated with the appropriate project/process owners to accomplish the project goals.
Encourage and drive the development of a culture of safety, Lean, quality, 6S and continuous improvement mindset amongst all co-workers.
Encourage and drive the development of an engaged and empowered workforce through ongoing leadership and support.
Ensure two-way open communication throughout the organization. This includes keeping the stakeholders informed of program status and ensuring coordination of activities.
Remain current with state-of-art quality-based strategies, programs, tools and ISO compliance and implement quality techniques throughout the organization.
Develop Caban's continuous improvement roadmap.
Establish and support a work environment of continuous improvement that supports relevant compliance regulations
The area of responsibility includes the authority and responsibility to initiate action to prevent the occurrence of any non-conformity relating to product, process, and quality systems
Identify and document problems relating to the product, process, and/or quality system. Initiate, recommend, and provide solutions through designated channels
Verify the implementation of solutions and controls to mitigate further processing or delivery of nonconforming product until deficiencies or unsatisfactory conditions have been corrected
Provide leadership / mentoring / training to project teams on the use and practice of Lean methodologies and tools
Assure that practices promoting continuous improvement are adopted by the organization to drive improvements in morale, quality, delivery and cost
Perform other duties and/ or responsibilities as assigned
Requirements
Bachelor's degree in Industrial Engineering, Supply Chain Management, Engineering, Logistics, Business Administration
Additional certification in Program Management or Project Management preferred
3 years experience in Lean/Operations Excellence role, preferably in a technology manufacturing organization
Ability to deal tactfully and confidently with external customers at all levels
Previous project management experience and Lean-based principles/tools (i.e. Value Stream Mapping, Cell Design and Material Flow, Visual Factory and Gemba walks, Standard Work, 6S, SMED)
ISO compliance and audit experience, preferably in a high tech manufacturing environment
Experience leading business transformation initiatives
A working knowledge of an ERP system is preferred
Experience managing corrective actions systems
Poise and ability to act calmly and competently in high-pressure, high-stress situations and excellent interpersonal skills
Proficient in the use of problem-solving tools, performing root cause analysis and implementing corrective actions
Excellent business acumen
All qualified candidates will receive consideration for employment without regard to race, color, religion, sex, gender identity, sexual orientation, national origin, disability, or protected veteran status.