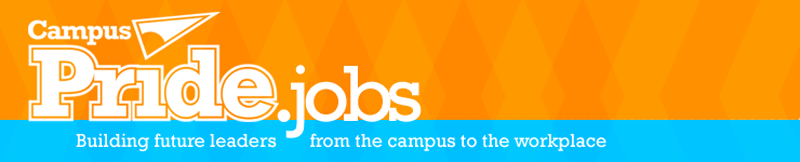
Job Information
ManpowerGroup Maintenance Planner/Scheduler in Pasadena, Texas
Maintenance Planner/Scheduler
Overview
Support proactive maintenance processes by effective and efficient planning and scheduling of all proactive and non-emergency work. This role will lead the long-range scheduling process as well as developing detailed plans and/or packages for non-emergency work. This includes planning outage work and developing outage schedules. Works directly in SAP with the maintenance team to help maintain maintenance data as well as making improvements to job procedures. Additionally, this individual will play a key role in the PdM program and help implement equipment strategies.
This position plans, schedules and maintains work for the site for all crafts, excluding emergent work notifications which are processed by the Maintenance Supervisor and Coordinators. The role is responsible for converting all notifications to orders, field planning, major parts ordering through the requisition and/or stores reservation process, constructing and refining an equipment planned work library, production of a weekly maintenance schedule, scheduling, and organization of the PM program, managing the maintenance backlog for accuracy, publishing of planning and scheduling KPIs, and building of detailed outage plans and schedules.
Job Scope
This position is responsible for and owns the processing of all work requests from submission through completion and TECO including all work order system controls and backlog management. Processing includes detailed planning of the work as well as scheduling, completion, and any required follow-up. Planning includes fully understanding the scope of the required work, constraints of having access to the equipment, and work preparation. Planning includes determining all the necessary materials, labor, and services needed to safely complete the work. All work must be planned with the intent of archiving the written plans such that the plans are retrievable for all future work. Scheduling includes producing a weekly schedule which has status continuously updated during execution considering break in work and discovery which impact the plan. This position is expected to spend considerable time in the field physically planning jobs and confirming the work with stakeholders. Works closely with the site warehouse to ensure spare parts stock and stock quantities support normal repair activities.
Responsibilities
• Produces a weekly maintenance schedule.
• Maintain all SAP maintenance master data in accordance with MOC’s such as: bill of materials, equipment records, spare part identification, functional location updates, maintenance strategies, maintenance plans, task lists, work centers, maintenance items, and WO attachments.
• Order major repair materials for planned work through direct POs or via stores reservations.
• Build new and update individual equipment BOMs as necessary.
• Publish and track planning, scheduling, and work execution KPIs weekly.
• Scope and compile job packages for all planned work including labor requirements, tools, parts and materials, procedures, equipment, permits, or any other resources required for a job.
• Create follow-up work orders from PdM reports. Work closely with the Reliability Engineers to evaluate findings from PdM reports and determination of corrective next steps.
• Coordinate with operations and production planning to execute long range scheduling of proactive work and equipment outages.
• Produce detailed outage plans and schedules (typically 2 larger outages per year). These consist of standardized base outage PM plans, planned vessel inspections, and backlog corrective maintenance.
• Maintain an accurate work backlog by craft which considers all planned and unplanned orders as well as approved notifications.
• Update the PM program design to ensure PMs for major equipment have all minor related PMs linked so all PMs are completed when the major equipment is made available.
• Optimize all routine work using BOM’s and task lists. Analyze feedback received from crafts to adjust labor hours to optimize planning efficiency (compare actual vs. planned hours).
• Prepare reports and update task lists as necessary.
• Work with storeroom coordinator to update material masters and generate stock change requests for new/existing spare parts inventory.
• Participate in equipment reliability strategy development which follow Reliability Centered Maintenance (RCM) strategies.
• Maintain and update filing of appropriate maintenance records, either manually or using a computer.
• Compile, copy, sort, and file records of office activities, project documentation, equipment history and other data.
• Work with maintenance leadership to drive continuous improvement for maintenance work processes.
• Included in the department’s on-call salaried rotation schedule.
Education & Experience Minimum
• High School degree and at least three years of maintenance or project planning experience in an industrial environment
• Equivalent combination of experience and education can be substituted for the requirements above.
• Proficient with Microsoft Office Suite primarily Word, Excel, and PowerPoint software.
• Experience in using SAP Plant Maintenance basic functions.
Education & Experience Preferred
• 3-5 years of maintenance planning experience and/or associate degree.
• Demonstrated working knowledge in effectively utilizing SAP Plant Maintenance and Materials Management modules related to notifications, orders, preparing schedules, reserving warehouse materials.
• Previous experience with turn around / plant outage planning.
• Working knowledge of all craft disciplines including millwright/mechanical, pipefitting, electrical, instrumentation, painting, insulation, and scaffolding.
Essential Competencies
• Accuracy – Ability to perform work accurately and thoroughly.
• Communication, Oral – Ability to communicate effectively with others.
• Communication, Written – Ability to communicate in writing, clearly and concisely.
• Customer Oriented – Ability to take care of the customers’ needs while following company procedures.
• Detail Oriented – Ability to pay attention to the minute details of a project or task.
• Teamwork – Ability to exhibit a cheerful demeanor toward others and work effectively in a team environment.
• Honesty/Integrity – Essential to be viewed as credible in the workplace.
• Initiative – Ability to make decisions or take actions to solve a problem or reach a goal.
• Organized – Possessing the trait of being organized or following a systematic method of performing a task.
• Relationship Building – Ability to effectively build relationships with stakeholders and co-workers.
• Self-Motivated – Ability to be internally inspired to perform a task to the best of one’s ability using his or her own drive or initiative.
• Learning Capacity – Ability to learn and apply new knowledge and skills.
ManpowerGroup is committed to providing equal employment opportunities in a professional, high quality work environment. It is the policy of ManpowerGroup and all of its subsidiaries to recruit, train, promote, transfer, pay and take all employment actions without regard to an employee's race, color, national origin, ancestry, sex, sexual orientation, gender identity, genetic information, religion, age, disability, protected veteran status, or any other basis protected by applicable law.