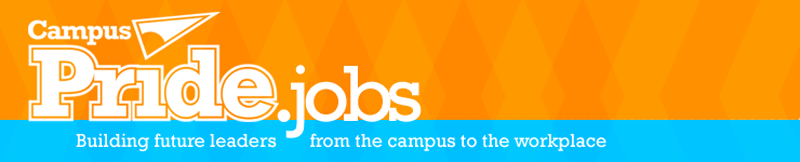
Job Information
Kaiser Permanente Senior Manager, Facility Engineering in Ontario, California
Job Summary:
Leads coordination efforts of facility engineers to provide preventative maintenance and repairs services for facility equipment (e.g., central plant operations, building management systems, safety systems). Drives teams responses to highly complex, long-term requests for repairs and troubleshooting of facilities equipment. Monitors and documents the scheduled preventative maintenance to ensure maintenance is carried out in accordance with regulatory requirements. Establishes processes for the entire team to ensure that facilities equipment passes safety checks and inspections in accordance with safety control programs (e.g., infection control, Material Safety Data Sheets [MSDSs], chemical control, fire safety, Emergency Care Research Institute [ERCI] alerts, and The Joint Commission (TJC) related programs, and all local regulatory requirements). Contributes to program-level goals for maintenance and repairs performed. Drives team to manage vendors to identify improvements for performing services out of scope for Facility Engineering team.
Essential Responsibilities:
Creates and advocates for developmental opportunities for others; builds collaborative, cross-functional relationships. Solicits and acts on performance feedback; works with leaders and employees to set goals and provide open feedback and coaching to drive performance improvement. Pursues professional growth; hires, trains, and develops talent for growth opportunities; strategically evaluates talent for succession planning; sets performance management guidelines and expectations across teams / units. Oversees implementation, adapts, and stays up to date with organizational change, challenges, feedback, best practices, processes, and industry trends; shares best practices within and across teams. Fosters open dialogue amongst team members, engages, motivates, and promotes collaboration within and across teams; motivates teams to meet business objectives. Delegates tasks and decisions as appropriate; provides appropriate support, guidance and scope; encourages development and consideration of options in decision making; fosters access to stakeholders.
Manages designated units or teams by translating business plans into tactical action items; oversees the completion of work assignments and identifies opportunities for improvement; ensures all policies and procedures are followed; partners with key stakeholders and business leaders to ensure products and/or services meet requirements and expectations while aligning with departmental strategies. Aligns team efforts; builds accountability for and measuring progress in achieving results; assumes responsibility for decision making; fosters direct reports to resolve escalated issues as appropriate. Communicates goals and objectives; incorporates resources, costs, and forecasts into team and unit plans; ensures matrixed resources are fulfilling service or performance requirements across reporting lines. Removes obstacles that impact performance; identifies and addresses improvement opportunities; guides performance and develops contingency plans accordingly; influences teams and units to operate in alignment with operational and business objectives.
Employs new and updated facilities equipment (e.g., central plant operations, building management systems, safety systems) by: overseeing installation of new equipment, updates to existing equipment, and user training on proper operation and potential hazardous or safety issues; driving team as necessary to leverage and optimize processes for the acquisition of operations and technical service manuals; contributing to the criteria for and evaluating the need for new and updated equipment in the present and future; and documenting the unique IDs for devices, creating a record in the database management system, and providing guidance to junior team members to do the same.
Ensures compliance with regulatory requirements for preventative maintenance by: providing guidance on complex safety and maintenance initiatives; monitoring and documenting the progress of teams performing preventative maintenance (PM); leading coordination efforts with outside resources as appropriate to ensure compliance with regulatory requirements; and overseeing the allocation of resources.
Plans, coordinates, and supervises long-term equipment maintenance (e.g., central plant operations, building management systems, safety systems) by: driving teams responses to highly complex, long-term requests for maintenance; ensuring teams have necessary outside resources for a variety of repairs, including complex repairs with long-term implications; and providing guidance and coordinating across organizational lines.
Promotes a safe environment by: driving individuals to complete safety tasks, including inspecting safety of equipment and/or facilities; participating in safety control programs to build on in-depth knowledge in one or more specialty areas (e.g., infection control, Safety Data Sheets [SDSs], chemical control, fire safety, Emergency Care Research Institute [ERCI] alerts, The Joint Commission [TJC] related programs, and other hospital-related regulatory agencies); and establishing processes for the entire team and ensuring proper documentation in the centralized maintenance management system while preparing the team for future safety needs.
Contributes to vendor relationship management by: assessing current operational processes on an on-going basis while driving team to manage vendors, including vendor assessment, performance analytics, and relationships to highlight trends and identify highly impactful and far-reaching process improvements that increase efficiency and effectiveness of vendor management; and driving the management team to improve the efficiency of vendor maintenance/service and reduce reliance on vendors through education and training.
Minimum Qualifications:
Bachelors degree in Engineering or technical disciplines in Plant Operations, HVAC, Electrical, Plumbing, or related field AND minimum seven (7) years of experience in Engineering, Plant Operations, HVAC, Electrical, Plumbing, or a directly related field OR Minimum ten (10) years of experience in Engineering, Plant Operations, HVAC, Electrical, Plumbing, or a directly related field.
Drivers License (in location where applicable)
Additional Requirements:
Knowledge, Skills, and Abilities (KSAs): N/A
COMPANY: KAISER
TITLE: Senior Manager, Facility Engineering
LOCATION: Ontario, California
REQNUMBER: 1310140
External hires must pass a background check/drug screen. Qualified applicants with arrest and/or conviction records will be considered for employment in a manner consistent with Federal, state and local laws, including but not limited to the San Francisco Fair Chance Ordinance. All qualified applicants will receive consideration for employment without regard to race, color, religion, sex, national origin, sexual orientation, gender identity, protected veteran, or disability status.