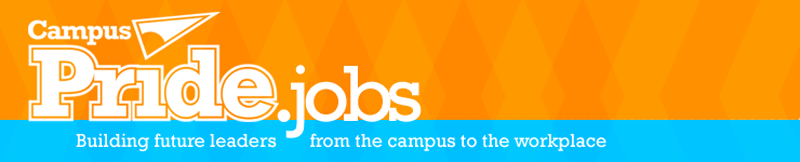
Job Information
Radius Packaging Shift Manager - Nights in New Berlin, Wisconsin
At Radius Packaging, we prioritize our employees' growth, collaboration, and well-being. Our culture is rooted in our Values and Guiding Principles - The Radius Way: Champion Positive Change, Act with Integrity, Strive for Excellence, Emphasize Community, and Work Together.
We are a recipient of the Plastics News Excellence in Employee Relations Award, which recognized us for our commitment to fostering a supportive workplace environment and nurturing a strong company culture. We were specifically honored for our continuing education initiatives, recognition programs, engaging employee events and opportunities for career advancement. Radius Packaging was also recognized as a Top Workplace by the Milwaukee Journal Sentinel in 2024.
At Radius Packaging our relentless focus on innovation and operational excellence are just some of the reasons our customers enjoy working with us. Our unique company culture, progressive leadership and dedicated members mean that who we are is just as important as what we do. For fifty plus years, we've had fun supplying plastic packaging for diverse consumer and commercial markets. Our members are known for creating and delivering products that they care about. So you can expect that we exceed industry standards for quality and durability, and you'll be working with members who go the extra mile to help our customers and our business remain successful. From containers for food, beverage and personal care products, to household and industrial chemicals, we continue to enhance our product offerings to be a full scope packaging provider. We are based in New Berlin, have a second facility in Delavan and a warehouse located in West Allis with approximately 260 members.
We are currently seeking a motivated Night Shift Manager for our New Berlin location. This position will report to the Plant Manager. The ideal candidate will have prior manufacturing management experience, preferably in plastics and will play a key role in the success of the organization by driving operational execution of daily production in several key areas of the business: Safety, Quality, Cost, Delivery, Production OEE, Member Engagement, and Continuous Improvement. In the quest for innovation, the Shift Manager will strive to improve their work, our team, and our environment through genuine leadership, a positive attitude and open communication, using a safe, practical, hands-on approach to teamwork.
Radius Packaging offers many great benefits including medical, dental and vision insurance, vacation, company paid holidays, 401(k) & company match, bonus potential, company paid life insurance and disability, FSA health & dependent care flexible spending accounts, health savings accounts, Teledoc, training and development opportunities, referral bonus program, complimentary hot beverages and more.
This position will have oversight of the Process Improvement Leader, Line Operators, Machine Technicians and Material Handler/Forklift Operators on their designated shift.
The schedule for the Shift Manager will be a 3-day per week 12-hour shift rotation. As the leader overseeing the rotation, you are required to be onsite in advance of the shift starting and after the shift ends for a shift handoff. The shift runs from 6:45pm-7:00am. The Shift Manager will also be required to participate in weekly, monthly and quarterly meetings, reviews and training and is expected to work a minimum of 40+ hours per week even though the shift rotation is less than 40.
In this role you will:
Lead by example, ensuring a safe and efficient workplace is maintained at all times.
Drive the execution of the monthly and daily production plan, working cross-functionally to ensure consistent efficiency in material movements and production within the established budget.
Plan and Budget the shift labor staffing and aid in managing technical assignments to ensure best utilization and development of talent on the team.
Coordinate and work with outside agencies and Human Development to bring in additional team members as business needs fluctuate.
Ensure all running machines are staffed by priority.
Oversight, monitoring, directing and maintaining the cleanliness of the plant.
Minimize the overtime incurred and maintain OT below customer communicated requirements.
Acclimate and communicate job, departmental and other work-related requirements to new members and temporary members and ensure they are trained on safe work practices.
Promote, Identify and actively engage in continuous improvement efforts throughout the organization. Drive CI & 6S programs, educating floor leaders and their team members while driving improvement and change.
Enter work orders, escalate ongoing issues, prioritize repair activity and remove barriers to completion for the team.
Monitor and ensure effective packaging material availability and staging to support production OEE, quality and safety.
Monitor and manage best cost utilization of materials such as regrind usage, reduced cold melt creation and scrap reductions.
Compliance to GMP, Food Safety, and Food Quality regulations as required by the company, customers, and/or government agencies.
Always be willing to help other support other teams with open tasks and projects.
Monitor the condition of equipment, request repairs via workorder management systems, and improve the equipment outputs through operations management and maintenance teams to support uptime and remove barriers to member productivity.
Work with the Safety leader to audit and ensure effective adherence to safety programs and overall safe environment and behaviors on the production floor, including involvement in performing assessments and driving completion of observations by the team. Actively participate in incident and near miss reporting and reviews for corrective actions.
Work with the Quality team to ensure production of quality products, making decisions that drive consistent processes and checkpoints that ensure customer requirements are met.
Work with Human Development to identify opportunities for training and developing our members.
Participate in the recruitment and selection of new team members and ensure new team members are successfully onboarded and trained within their designated function.
Lead and coach providing direction, managing performance, and developing leaders to enable engagement and retention of key talent.
Review and administer attendance consistent with policies for all team members.
Undertake performance management responsibility for team members, conducting appraisals and giving direction to aid good performance, holding members accountable and administering corrective actions when necessary.
Communicate openly and proactively throughout the team to promote a culture of inclusion, empowerment, growth and connectivity for all members.
Promote participation by all members in company initiatives and programs, including production floor processes, organization and cleanliness. Ensure all members are following Food Safety standards and workforce policies.
Identify and direct special projects needed – ie. Rework / repack.
Qualifications
Bachelor’s degree in Operations, Engineering or Business with 3 years of progressive leadership in a manufacturing organization, without a degree, 5 years of leadership required, preferably in a plastics processing environment.
Demonstrated capability to lead continuous improvement programs in manufacturing processes and practices, preferably in a plastics manufacturing environment.
Proficient in the usage of Microsoft Office Programs (Excel, Word, PowerPoint, TEAMS)
Experience with using MRP or ERP systems to manage materials, inventory and production scheduling.
Familiarity with the usage of Apple Devices and software preferred.
Evidence of credible coaching leadership style with the ability to inspire and lead high performing technical teams.
Excellent, proactive and real time communication skills – casual and formal, oral and written.
Demonstrated focus on member safety, above all, and quality production when safety requirements are met.