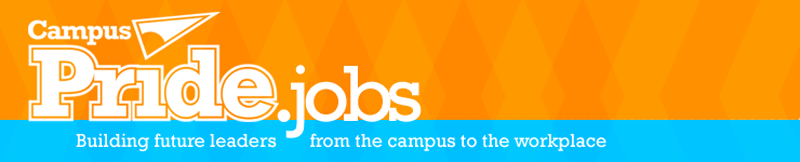
Job Information
Genpak LLC Shift Mechanic - Nightshift - Kilgore in Kilgore, Texas
::: {tabindex="0"}
::: {testid="vjJobDetails-test"}
Job details
Shift and schedule
12 hour shift Overtime
Benefits
- 401(k) matching
- Dental insurance
- Health insurance
- Paid holidays
- Tuition reimbursement
- Vision insurance
Full job description
:::
Maintain all equipment/machinery and building in good working order and repair as necessary.
ESSENTIAL DUTIES AND RESPONSIBILITIES:
- Must be able to work the "Shift Work schedule" which includes every other Sunday.
- Provide and maintain appropriate tools and toolbox to perform all necessary job functions.
- Coordinate all job assignments with Shift Supervisor at start of shift to ensure maximum production uptime and efficiency.
- Assist Shift Supervisor with proper facility evaluation procedures including machinery shutdown.
- Oversee and coordinate PM Operator functions for the respective shift.
- Excellent understanding of pneumatics, electrical controls and hydraulics with ability to diagnose and correct problems.
- Application of strong mechanical and electrical knowledge including such as abilities in reading of schematics, etc.
- Perform assigned Preventive Maintenance/ Safety Programs per defined schedule with accurate and complete documentation.
- Complete all assigned Work Orders in a timely manner.
- Maintain Maintenance Parts Inventory per Infor and Plant Sanitation standards including:
- ensuring tag is pulled and turned in when part is pulled out of inventory
- recording correct parts used on all work orders
- parts are re-stocked in appropriate location per Infor System
- Able to breakdown and setup all Extrusion and Thermoforming product on machinery to standards set including:
- knowledge of quality/operational standards per product
- quality inspections performed
- work area cleaned
- ensuring that tooling is in good working condition prior to setup
- cleaning, maintenance and proper storage of tooling upon breakdown
- Full understanding of extrusion and thermoforming process and machinery to ensure quality production uptime including:
- diagnosing of problem (microphraser control panel, dies, ovens, trim press, etc.)
- repair of problem with little to no supervision to ensure maximum production run time.
- Adjustment to daily schedule (break times, meal periods, etc.) to ensure machinery in back in full production to maximize production uptime.
- Perform all facility shutdown and startup procedures correctly and completely including incinerator, etc.
- Perform necessary repairs to building including but not limited to:
- plumbing
- roof
- silos
- trenches
- heating and air systems
- dock doors and plates
- chiller system
- parking lot
- building additions/renovations
- equipment modifications
- new equipment installations
- Follow Hot Work Permit procedures and ensure proper documentation is completed and signed off by Maintenance Manager/Shift Supervisor.
- Operate all PIT equipment per OSHA specifications, including daily inspections, changing of batteries/propane tank, etc.
- Perform all housekeeping functions necessary to business operations (from daily shift requirements to Plant Sanitation audits) in respective work areas at all timesl.
- Perform all "end of shift" job functions including:
- Communicate all equipment and material issues arising from the operation of the shift with on-coming Maintenance personnel and/or Shift Supervisors/Maintenance Manager at each shift change.
- Clean and organize work area
- All maintenance parts and tools are properly stored
- Breakroom is neat and clean
- Unload "incoming" product/material for receipt and placement into facility as business demands.
- Assist in b ilding/machinery preparation of all Plant Sanitation/OSHA audits.
- Work overtime as business demands, including monthly training classes as mandated by OSHA and Plant Sanitations Certifications.
- Comply with all company policies and procedures, including all safety regulations.
- Perform any and all job assignments/functions (including special projects) as necessary to daily business demands as instructed by Management.
The Company has the right to alter or add job functions to meet business demands as necessary.
Requirements:
EDUCATION and/or EXPERIENCE:
High school diploma or general education degree (GED
3 years experience of manufacturing maintenance experience to include: welding, trouble-shooting of pneumatics, hydraulics, electrical controls, and maint
:::