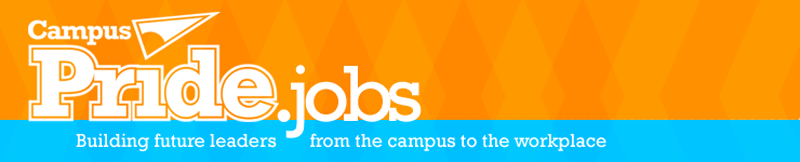
Job Information
Amentum Corrosion Control System Engineer in Kennedy Space Center, Florida
Company Conformance Statement
In the performance of their respective tasks and duties all employees are required to conform to the following:
Perform quality work within deadlines with or without direct supervision.
Interact professionally with other employees, customers, and suppliers.
Work independently while understanding the necessity for communicating and coordinating work efforts with other employees and organizations.
Employees are required to:
Comply with all applicable safety and health-related rules, regulations, and procedures.
Work safely themselves and help their teammates work safely.
Assist supervisors and other managers in identifying and mitigating potentially hazardous conditions.
Help the organization maintain a safe and healthy workplace.
Purpose and Scope
The Corrosion Control System Engineer is the subject matter expert in cathodic protection, protective coatings and linings, materials selection, and condition assessments. The engineer will analyze the corrosivity of the environment, perform field tests and surveys, develop alternatives for corrosion control within established design criteria, design the preferred corrosion control systems, specify materials and coatings, and support construction. The individual will have minimal oversight and be responsible for developing and maintaining a center-wide corrosion control plan to support all Launch and Mission related activities and assets.
Job Duties and Essential Responsibilities
System Specific
Create control plans and put in place the framework for mitigations for assets and critical hardware Prepare detailed reports and presentations for clients to communicate corrosion risks, mitigation strategies, and progress Provides Materials Engineering consulting to engineers, management, and customer. Provides consultation on materials selection, corrosion monitoring and control, remaining service life assessment, and repair strategies. Develops and reviews technical specifications relating to materials and corrosion. Influence designs and maintenance plans to ensure the right materials, coatings, and protections get implemented that enable the long-term health and reusability in corrosion near ocean environments. Daily hands-on activities such as troubleshooting, developing procedures, conducting inspections, testing, and analyzing hardware Lead ECDA assessments for metallic structures and assets Work closely with field teams to ensure that ECDA assessments and cathodic protection designs are conducted safely and effectively Develop corrosion management strategies based on ECDA results and industry best practices Analyze assessment data to evaluate the integrity of assets and identify potential corrosion risks Design cathodic protection systems for metallic structures and assets, CP4 Cathodic Protection Specialist Certification preferred. Stay up to date with emerging technologies and industry trends related to corrosion engineering and cathodic protection
Maintenance
Revise and add new asset information in Maximo database for assigned equipment per MAR (Maintenance Action Request) process. Develop and maintain job plans and PMs for assigned equipment in accordance with launch and processing operations, NASA-STD-5008B and industry standard requirements. Address and justify preventive maintenance deferrals of assigned equipment. Conduct site visits to investigate system problems, propose solutions and provide recommendations to restore systems. Support shop technicians in troubleshooting issues related to assigned equipment as needed. Provide technical expertise for technical anomalies as they arise. Resolve and document failure anomalies regarding assigned equipment. Prepare Technical Anomaly reports and presentations documenting problems, concerns, and resolutions for assigned equipment to the Engineering Review Board.
Readiness
Develop and present or represent mission related presentations to the NASA and/or EGS customer as required to present support readiness or failure concerns. Perform readiness assessments of assigned equipment and systems.
Project Support
Coordinate and work closely with requester, customers, other engineering, logistics, financial, and program management disciplines to define system specifications and requirements. Direct interface and liaison with internal and external customers at all levels from concept to final design and commissioning activities, design reviews and technical working group meetings to comply with requirements and specifications. Support development of technical proposals, statements of work and/or provide comments on the technical content and level of effort of the proposed scope of work. Develop task order requirements to NASA to complete Operations & Maintenance Documentation (OMD) updates per specific, contracted timeframes. OMD updates could be on drawings or job plans for assigned equipment/systems. Coordinate and communicate effectively with CAD drafters, Design Engineers, or shop personnel by written or verbal means. Perform all other position related duties as assigned or requested.
Education and Experience Requirements
Bachelor’s Degree in Materials, Corrosion, Metallurgical Engineering, or related engineering field with an emphasis on corrosion and 2+ years of job-related experience or equivalent. 1+ years of experience in corrosion control, mitigation, or research (significant academic projects, internships, and traditional professional experience all qualify). Protective coatings and linings specification, inspection, and evaluation Condition assessment of facilities affected by corrosion Knowledge of industry standard computer software for the position (examples include software such as CADD, AutoCAD, MicroStation, SKM, ETAP, PLC interface software, etc.). Practical work experience in corrosion control coatings, inhibitors, paints or/and electrochemistry on facilities, equipment, or other real-world applications. NACE Certified Corrosion Specialist preferred NACE Certified Cathodic Protection Specialist, or Registered Professional Corrosion Engineer preferred API certifications in 510, 570, 580, and 571 preferred Working Knowledge of PLC control logic diagrams preferred Cathodic protection system planning, design, operation, and analysis preferred
Preferred Qualifications:
May require some limited travel. May require the ability to pass and maintain a Security Clearance.
Required Minimum Position Knowledge, Skills, and Abilities:
Ability to exercise sound judgement and reason.
Strong ability to use data and analysis to make fast data-driven decisions.
Capable of using spreadsheets, word processing and standard Microsoft Office software to include Excel, Word, PowerPoint and Visio.
Ability to read and interpret documents such as safety rules, operating and maintenance instruction, and procedure manuals.
Ability to read and understand schematics & blueprints.
Ability to write routine reports and correspondence. Ability to speak effectively before groups of customers or employees of the organization.
Must possess general knowledge of office routines to include scheduling, general office administration, and a working knowledge of standard computer software.
Ability to apply common sense understanding to carry out instructions furnished in written, oral, or diagram form.
Other Requirements:
Must be a U.S. citizen and be able to obtain and maintain required Government clearances/badges as required by program and position
Must have the ability to communicate in English, both verbal and written in an effective manner.
Must have and maintain a valid driver’s license.
Work Environment, Physical Demands, and Mental Demands:
This position involves work typical of an office environment with no unusual hazards; occasional lifting to 20 pounds; constant sitting with use of computer terminal; constant use of sight abilities while reviewing documents; constant use of speech/hearing abilities for communication; constant mental alertness; must possess planning/organizing skills and must be able to work under deadlines. Field work will consist primarily of site walk downs in support of corrosion planning. Site hazard training and Personal Protective Equipment are provided.
Other Responsibilities:
Safety - PSP enforces a safety culture whereby all employees have the responsibility for continuously developing and maintaining a safe work environment. As appropriate, each employee is responsible for completing all training requirements and fulfilling all self-aid/buddy aid responsibilities, participating in emergency response tasks, and serving on safety committees and teams.
Quality - Quality is the foundation for the management of our business and the keystone to our goal of customer satisfaction. It is our policy to consistently provide services that meet customer expectations. Accordingly, each employee must conform to the PSP Quality Policy and carry out job activities in compliance with applicable PSP Quality System documents and customer contracts. Each employee must read and understand his/her Quality Management and Customer Satisfaction responsibilities.
Procedure Compliance - Each employee must read, understand, and implement the general and specific operational, safety, quality and environmental requirements of all plans, procedures and policies pertaining to their job.
Amentum is proud to be an Equal Opportunity Employer. Our hiring practices provide equal opportunity for employment without regard to race, religion, color, sex, gender, national origin, age, United States military veteran’s status, ancestry, sexual orientation, marital status, family structure, medical condition including genetic characteristics or information, veteran status, or mental or physical disability so long as the essential functions of the job can be performed with or without reasonable accommodation, or any other protected category under federal, state, or local law.
Labor Law Posters (https://postings.govdocs.com/#/vxSkbztPuAwwxfs)
EEO including Disability/Protected Veterans