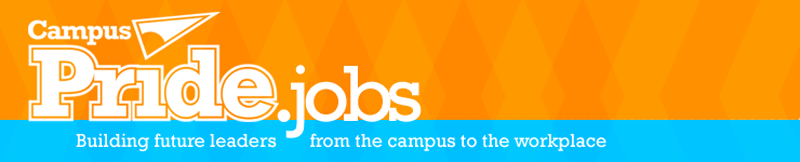
Job Information
Dairy Farmers of America Quality Control Technician - Night Shift in Joplin, Missouri
Job Description
Perform various quality assurance and quality control functions; ensure measuring equipment is accurate to determine that customer specifications are met. This position works the night shift which is 6:00 pm - 6:30 am.
ESSENTIAL FUNCTIONS/MAJOR RESPONSIBILITIES:
Exhibit Good Documentation and Laboratory Practices.
Perform online quality control checks of all production lines.
Determine Quantity Control Parameters. Monitor package fill volumes/weights to ensure compliance with label declarations.
Code verification of primary, secondary and tertiary packaging if applicable.
Perform quality control monitoring of lab and plant systems.
Monitor scales used for weight verification.
Perform environmental monitoring of production areas.
Monitor temperatures of equipment utilized for methods or processes in which temperature is a critical factor or step.
Maintain sample retention library.
Receive and track analytical reagents, thermometers and other laboratory supplies.
Change incubation room charts.
Perform general cleaning per laboratory sanitation requirements.
Recognize and respond to unexpected test results, errors and discrepancies.
Calibrate pH meters and perform pH measurement.
Ability to read and comprehend oral and written instructions and effectively communicate information in one-on-one settings.
Visual color discrimination, general vision of 20/40 or better with or without corrective lenses.
Employees are expected to act in a manner that is professional and appropriate for representing the company.
Perform any other work duties as assigned.
Requirements
Moderate on the job training.
High school diploma, GED or some technical training or certifications preferred.
Related experience and/or detailed administrative background a plus.
Physical Demands:
The quality lab tech pulls finished products from the line to ensure the quality of the product and its containers.
There is a cart that is pushed from the QA lab out to the lines. This cart requires 12 pounds to push at its heaviest. The product is placed on the top shelf of this cart, which is at 33 inches off the ground. Some of the product pulled will be put into a tub on another cart that is also 33 inches off the ground. These will eventually be put into an incubator room to check for bacteria growth. Others will be used to check the actual product or packaging of the product.
The products to be put into the incubation room are rolled on the cart as far as 160 feet. The cart requires 17 pounds of force to push when it is full. There are two tubs on the cart with 16 individual boxes of product in each tub. The heaviest the tub can be is 46 pounds. They have to be lifted from the 33-inch high cart to as high as 76 inches off the ground. They may have to lower down to 6.5 inches.
In some scenarios, the tubs would have to be carried a maximum of approximately 20 feet. The tub movements into or out of the incubation rooms occur approximately every 60 minutes. The incubation room is kept at 95 Degrees F.
Tubs are taken away from the incubation room the same as they are brought in.
There is a data sheet that is provided to the lab tech that has the product codes for the individual boxes and cases. The tech checks these codes on the individual product containers and on the cases as well.
An Equal Opportunity Employer
Pay Range $23.25 / hour