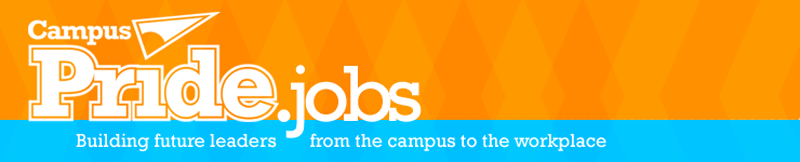
Job Information
Allison Transmission Senior Digital Transformation Engineer in Indianapolis, Indiana
JOIN THE TEAM THAT’S POWERING PROGRESS
Building cities. Driving commerce. Saving lives. For over 100 years, Allison Transmission has powered the vehicles and technology that move our world forward.What powers us? Our employees. From the first person hired by James Allison in 1915 to the thousands across the globe who work for Allison today, we’re driving progress everywhere because we employ top talent worldwide.
Learn more about this role and how you can begin driving your career forward!
Job Title:
Senior Digital Transformation Engineer
Pay Grade:
T3
Job Description:
Primary Purpose of Role:
We are seeking a highly motivated and skilled Digital Innovation Engineer to drive continuous improvement in our manufacturing operations using the Power Platform. In this role, you will leverage your technical expertise to streamline processes, enhance data analytics, and promote innovative solutions for the optimization of manufacturing operations.
Key Responsibilities:
Digital Transformation: Lead the digital transformation efforts in manufacturing operations, identifying opportunities for automation, process optimization, and enhanced data utilization.
Power Platform Expertise: Utilize the Power Platform to design, develop, and deploy custom applications, dashboards, and workflows to improve manufacturing processes and data-driven decision-making.
Continuous Improvement: Collaborate with cross-functional teams to identify areas for continuous improvement, cost reduction, and increased efficiency in manufacturing operations.
Data Analysis: Extract, transform, and analyze data to gain actionable insights, providing recommendations for process enhancements and performance optimization.
Project Management: Lead projects related to digital innovation, ensuring they are delivered on time and within budget, while also monitoring the impact on operations.
Training and Support: Provide training and support to manufacturing teams to ensure the successful adoption of digital solutions and Power Platform tools.
Compliance and Security: Maintain compliance with data security standards and industry regulations, ensuring the integrity of data and processes.
Documentation: Create and maintain documentation for developed solutions, processes, and best practices.
Key Performance Measures:
These KPIs can help assess the overall impact and effectiveness of the Digital Innovation Engineer in enhancing manufacturing operations and promoting continuous improvement using the Power Platform. It's essential to establish baseline measurements, set targets, and regularly review performance against these indicators to drive ongoing improvement.
Process Efficiency Improvement:
Percentage reduction in production downtime.
Increase in production output or throughput.
Reduction in defects, errors, or rework.
Percentage improvement in cycle time or lead time.
Digital Solution Deployment:
Number of successful applications, dashboards, or workflows developed and deployed using the Power Platform.
Time taken to implement and roll out new digital solutions.
Adoption rate of digital tools among manufacturing teams.
Data Utilization and Analysis:
Improved data accuracy and data quality.
Time saved on data collection and analysis.
Number of actionable insights generated from data analysis.
Cost Reduction and Resource Optimization:
Reduction in operational costs.
Optimization of resource utilization (e.g., materials, labor, energy).
Percentage decrease in maintenance costs.
Project Management:
Successful completion of digital innovation projects on time and within budget.
Effective management of project risks and issues.
Stakeholder satisfaction with project outcomes.
Training and Knowledge Transfer:
Assessment of the effectiveness of training provided to manufacturing teams.
Measurement of team's proficiency in using digital tools and Power Platform applications.
Compliance and Data Security:
Adherence to data security standards and industry regulations.
Number of security incidents or breaches (aiming for zero incidents).
Completion of required compliance audits and certifications.
User Feedback and Satisfaction:
Feedback from manufacturing teams on the usability and effectiveness of digital solutions.
Regular surveys or interviews to gauge user satisfaction and identify areas for improvement.
Documentation and Best Practices:
Maintenance and quality of documentation for solutions and processes.
Uptake of best practices in the team and organization.
Qualifications:
Required:
- Bachelor's degree in Engineering, Computer Science, or a related field.
Preferred:
Certifications in relevant areas such as Six Sigma, PMP, or Data Science.
Microsoft Power Platform certifications.
Experience:
Required:
5+ years experience in manufacturing operations and continuous improvement
3+ years experience with Microsoft Power Platform, including Power Apps, Power Automate, and Power BI.
Competencies and Behaviors:
For the role of a Digital Innovation Engineer for Manufacturing Operations with an emphasis on using the Power Platform, specific competencies and behaviors are crucial for success. Here's a list of key competencies and behaviors that are valuable in this role. These competencies and behaviors are essential for individuals in this role to effectively leverage the Power Platform and digital solutions to drive innovation and improvement in manufacturing operations. It's important to foster a culture of continuous learning and development to support these competencies and behaviors within the organization.
Competencies:
Technical Proficiency:
Mastery of the Microsoft Power Platform, including Power Apps, Power Automate, and Power BI.
Strong data analysis and visualization skills.
Understanding of manufacturing processes and technologies.
Understanding of relational databases
Problem Solving:
Ability to identify and analyze complex manufacturing challenges.
Innovative problem-solving skills to design effective digital solutions.
Project Management:
Project planning and execution skills to deliver digital initiatives on time and within budget.
Risk management and issue resolution.
Data Management:
Proficiency in data collection, transformation, and interpretation.
Data quality management and data security awareness.
Continuous Improvement:
Strong commitment to process optimization and a proactive approach to identify areas for improvement.
Knowledge of continuous improvement methodologies (e.g., Lean, Six Sigma).
Innovation:
Creativity and a passion for exploring and implementing new technologies and Industry 4.0 concepts.
Ability to adapt to emerging trends in manufacturing and digital solutions.
Communication:
Effective communication skills to convey technical concepts to non-technical stakeholders.
Active listening and collaboration with cross-functional teams.
Training and Support:
Skill in educating and supporting manufacturing teams in using digital tools and applications.
Patience and empathy in helping others adapt to change.
Behaviors:
Proactive Approach:
Taking initiative to identify opportunities for improvement without constant supervision.
Adaptability:
Willingness to adapt to changing technologies, processes, and priorities in a dynamic manufacturing environment.
Detail-Oriented:
Paying close attention to details to ensure data accuracy and precise problem analysis.
Team Collaboration:
Collaborating effectively with cross-functional teams, acknowledging diverse perspectives and expertise.
Ethical Responsibility:
Upholding data security and privacy standards and promoting ethical behavior in all digital initiatives.
Resilience:
Handling setbacks and challenges with a positive attitude and determination to find solutions.
Result-Driven:
Focusing on achieving measurable outcomes and continuous improvement in manufacturing operations.
Leadership Potential:
Demonstrating leadership qualities to influence and drive change within the organization.
Documentation and Knowledge Sharing:
Maintaining thorough documentation and sharing best practices and knowledge with colleagues.
Primary Location:
Indianapolis, IN
Additional Locations:
Allison Transmission is an equal opportunity employer. We have opportunities for all qualified applicants regardless of age, race, color, sex, religion, creed, national origin, disability, sexual orientation, gender identity/expression or veteran status.
If you are an individual with a disability or a disabled veteran requiring assistance and/or reasonable accommodations reviewing any of the careers information, please contact us at ati+ask4max@service-now.com .
Please note that Allison Transmission will make an offer of employment only to individuals who have applied for a position using our official application. Be on alert for possible fraudulent offers of employment. Allison Transmission will not solicit money or banking information from applicants.
Allison Transmission is the world’s largest manufacturer of commercial-duty automatic transmissions and hybrid propulsion systems. Our products are specified by more than 300 of the world’s leading vehicle manufacturers and are used in a range of market sectors—from bus, refuse and emergency to construction, distribution and defense.
Allison was founded in 1915 in Indianapolis, Indiana, where the company’s global headquarters is still located. We have approximately 1,400 dealer and distributor locations, employ more than 2,700 people around the world and our international presence spans more than 80 countries.
Allison Transmission is an equal opportunity employer. We have opportunities for all qualified applicants regardless of age, race, color, sex, religion, creed, national origin, disability, sexual orientation, gender identity/expression or veteran status.
If you are an individual with a disability or a disabled veteran requiring assistance and/or reasonable accommodations reviewing any of the careers information, please contact us at 317-242-5000.
Please note that Allison Transmission will make an offer of employment only to individuals who have applied for a position using our official application. Be on alert for possible fraudulent offers of employment. Allison Transmission will not solicit money or banking information from applicants.