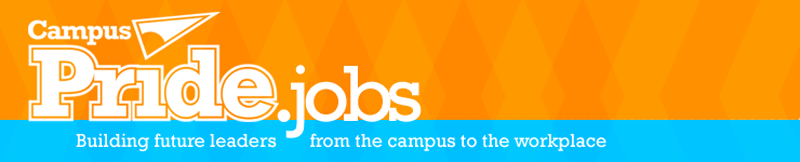
Job Information
Contract Pharmacal Corp Manager; Packaging Maintenance (1st Shift) in Hauppauge, New York
Manager; Packaging Maintenance (1st Shift)
Hauppauge, NY (http://maps.google.com/maps?q=135+Adams+Avenue+Hauppauge+NY+11788)
Apply
Description
Position Summary:
The Manager of Packaging Maintenance is responsible for supporting all packaging facilities to ensure equipment, documentation, facilities and support systems (i.e., HVAC, plumbing) are maintained, up to date, and in good working order.
Responsibilities: Include but are not limited to -
Member of Plant Leadership Team (Lock out, tag out program, fire and safety programs).
Monitor the use and inventory of spare parts, maintenance supplies, and equipment; initiate reordering when necessary.
Participate in objective setting, plan development and performance review.
Manage relationships with cross-functional teams to install, rebuild, or replace production equipment.
Manage plant maintenance support personnel.
Ensure that technical staff are adequately trained, equipped, and motivated so that technical work can be accomplished in a safe, timely, and cost-effective manner.
Work with engineering and suppliers to write and update equipment operation-based SOPs.
Review the operation of plant equipment and systems to minimize unplanned downtime, anticipate and solve problems in a timely manner, and identify opportunities for improvement.
Initiate and carry out projects that improve efficiency and/or reduce operating costs.
Track, analyze and improve key maintenance parameters such as asset utilization, maintenance cost, PM compliance, schedule compliance, etc.
Manage and schedule the preventive maintenance program, in addition to work order system.
Generate exceptional training and reference documents related to equipment operation and change over.
Perform center lining and 5S work to production lines, product contact parts, and change parts.
Maintain safety, health, and environmental policies and procedures.
Issue equipment-related Change Controls.
Manage maintenance mechanics and technicians training, ensure personnel are adequately equipped and motivated so the maintenance objectives can be accomplished in a safe, timely, and cost-effective manner.
Track, analyze and improve key maintenance parameters such as asset utilization, maintenance cost, PM compliance, schedule compliance, etc.
Maintain and repair maintenance shop equipment.
Prepare reports, analyze data, and make recommendations for improving facility operations and solving maintenance-related problems.
Initiate and carry out projects that improve efficiency and/or reduce operating costs.
Responsible for compliance with all rules and regulations pertaining to safety policies and for leading by example with the proper attitude toward safety and health, helping to ensure that all department operations are performed with the utmost regard for the safety and health for all personnel.
Other responsibilities as assigned by Senior Management.
Requirements
Education and Experience:
High school or GED diploma required.
Bachelor’s degree preferred.
Minimum 10 years of experience in mechanics and electrical preferably in pharmaceutical manufacturing.
Skills, Abilities and Knowledge:
Knowledge of Computerized Maintenance Management System (CMMS).
Expert knowledge of packaging equipment and facility support systems.
Basic business writing and computer skills.
Ability to effectively communicate expectations to employees.
Physical Demands:
Required to sit and stand for long periods of time.
Frequently reaching with arms/hands up to 2 feet.
Required to use hands and fingers to feel, handle or operate controls.
Good hand eye coordination.
Occasionally required to walk and kneel.
Must be able to lift and/or move up to 50 pounds.
Must be able to use close vision, distance vision, peripheral vision, color vision and the ability to adjust focus.
Required to reach with arms and use hands and fingers to handle or feel objects and tools.
Required to stoop, kneel, crouch, stand, bend, sit, talk, hear, climb stairs and ladders.
Work Environment:
Work environment in production operations facilities include close proximity to heavy machinery and pharmaceutical powders.
Potential to move between production operations sites/areas to complete job functions.
Hours/Travel maybe subject to changed based on management/company discretion.
Indoor manufacturing environment including enclosed areas with dust and loud noises.
Supervisory Responsibilities:
May supervise union and non-union employees.
Personal Protective Equipment or Attire Required for Position:
As needed.