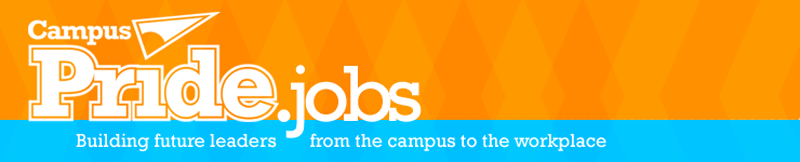
Job Information
RESILIENCE US INC Operational Readiness Leader in Hamilton, Ohio
A career at Resilience is more than just a job - it's an opportunity to change the future. Resilience is a technology-focused biomanufacturing company that's changing the way medicine is made. We're building a sustainable network of high-tech, end-to-end manufacturing solutions to better withstand disruptive events, serve scientific discovery, and reach those in need. For more information, please visit www.resilience.com Brief Job Description The Operational Readiness Leader is a pivotal role within the biopharmaceutical manufacturing organization, responsible for ensuring seamless integration and startup of new facilities, equipment, and processes. This leader will oversee operational readiness initiatives, ensuring compliance, efficiency, and alignment with industry standards. The ideal candidate will leverage cross-functional collaboration, technical expertise, and project management skills to deliver readiness plans that enable successful manufacturing operations. Job Responsibilities Operational Planning and Strategy: Develop and execute comprehensive operational readiness plans for new or updated manufacturing facilities, equipment, and systems. Collaborate with cross-functional teams (e.g., engineering, quality, validation, and production) to align project objectives with operational goals. Assess risks and develop mitigation strategies to address operational challenges during project execution and startup phases. Leadership and Collaboration: Lead cross-functional teams to ensure alignment on timelines, deliverables, and operational requirements. Act as a key liaison between project teams, stakeholders, and site operations to facilitate smooth transitions from project completion to steady-state operations. Process and Systems Implementation: Oversee the implementation and validation of manufacturing processes, equipment, and supporting systems to ensure readiness for GMP (Good Manufacturing Practice) production. Collaborate with engineering and technical services teams to develop Standard Operating Procedures (SOPs), training materials, and work instructions. Training and Workforce Readiness: Coordinate training programs for production staff to ensure competence in new equipment, processes, and systems. Develop and maintain a framework for ongoing operational excellence and continuous improvement. Regulatory and Quality Compliance: Ensure all operational readiness activities align with regulatory requirements and company quality standards. Support audits and inspections, providing documentation and insights into operational readiness activities as needed. Performance Monitoring: Track and report on key performance indicators (KPIs) related to operational readiness and project success. Identify and implement lessons learned to improve future readiness efforts. Minimum Qualifications: Strong understanding of GMP manufacturing principles and regulatory requirements (e.g., FDA, EMA). Proven experience leading facility startups, equipment commissioning, and process validation within regulated environments, particulary in biopharmaceutical manufacturing Expertise in project management tools, methodologies and best practices, with a demonstrated ability to deliver complex projects on time and within budget. Solid experience in lean manufacturing and continuous improvement methodologies to drive operational efficiency Excellent leadership skills with a demonstrated ability to lead, mentor and motivate cross-functional teams Strong communication skills, with the ability to effectively manage stakeholders and navigate complex organizational structures. Analytical and problem-solving capabilities to address changellenges and drive improvements. Ability to think strategically, balance long-term objecti