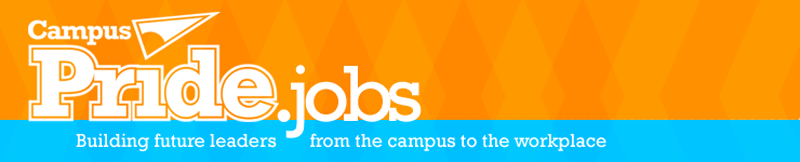
Job Information
Pactiv Evergreen Plant Engineering Maintenance Manager in Greensboro, North Carolina
Overview
Pactiv Evergreen Inc. (NASDAQ: PTVE)is a leading manufacturer and distributor of fresh foodservice and food merchandising products and fresh beverage cartons in North America and certain international markets. It supplies its products to a broad and diversified mix of companies, including full service restaurants and quick service restaurants, foodservice distributors, supermarkets, grocery and healthy eating retailers, other food stores, food and beverage producers, food packers and food processors. To learn more about the company, please go to the company website at pactivevergreen.com.
42 miles east of Winston-Salem, Greensboro is a city in North Carolina. The Greensboro Science Center houses red pandas, sharks and a hands-on museum. Nearby, Guilford Courthouse National Military Park has displays on the American Revolution. Video re-enactments and interactive exhibits trace the civil rights struggle at the International Civil Rights Center & Museum. The Bog Garden is a wetlands area with flowers, birds and an elevated boardwalk.
The plant was built in 1977 manufactures polystyrene foam protein trays, and has approximately 190 employees. In 2015, The Greensboro facility received an award from the State of North Carolina for working over one million hours without an OSHA lost time.
Pactiv Evergreen is committed to a diverse and inclusive workforce. Pactiv Evergreen is an Equal Opportunity Employer. All qualified applicants will receive consideration for employment without regard to race, color, sex (including pregnancy), sexual orientation, religion, creed, age national origin, physical or mental disability, genetic information, gender identity and/or expression, marital status, veteran status or other characteristics or statuses protected by law. For individuals with disabilities who would like to request an accommodation, please call (847) 482-4320 or email TalentHelp@Pactiv.com.
All information will be kept confidential according to EEO guidelines and applicable laws.
Our Social Responsibility platform features a robust, employee-led Give Back program, which includes a matching gifts plan, community grants initiative, and our annual Company-wide Month of Action campaign. With each of these initiatives, our employees are empowered and equipped to give back to their communities and support the non-profits important to them and their families. Through our Give Back program, we own our commitment to Social Responsibility and live our purpose of Packaging a Better Future.
Responsibilities
Summary:
Direct, manage, and coordinate the activities of the Maintenance and Tooling Department. Continuously improve and coordinate plant preventative/predictive maintenance program. Support initiatives to optimize and improve equipment.
Essential Duties and Responsibilities include the following:
Maintain a safety culture within the Maintenance and Tooling Department that positively influences safety efforts outside the Maintenance and Tooling Department and helps reduce safety incidences. Conduct safety meeting, accident investigations, and conduct safety training.
Develop applicable safety requirements and provide safety oversight to ensure compliance. Work with the EHS Manager to develop LOTO Program requirements.
Maintain an effective training program for Maintenance and Tooling Department employees and all other employees required to participate in any preventive/predictive maintenance (PM) activity.
Maintain an effective PM program. Train and interact with non-Maintenance Department employees as needed to ensure PM compliance.
Coordinate setup schedule and work assignments utilizing Maintenance Connection to assign job tasks and review work activity.
Work closely with employees to troubleshoot plant equipment including but not limited to support for processing and tooling maximization.
Coordinate with other departments and personnel as needed to ensure safe and correct equipment performance, and achievement of maximum up time and efficiencies.
Work closely with engineering on projects.
Ensure equipment downtime, due to equipment failure or PM, does not exceed current downtime standard.
Identify equipment failure caused by improper care or use and provide appropriate corrective action.
Staff appropriately to ensure full and continuous production operations.
Assists and leads in department activities aimed at increasing up-time through establishment of preventive maintenance and predictive maintenance programs.
Conceives and implements reliability improvement ideas.
Act as a lean champion.
Perform managerial duties including evaluations, disciplinaries, and other items in conjunction with Human Resources.
Back up to Technical Manager
Product Safety:
It is the intent, objective, and philosophy of PTVE to produce safe, legal, and quality products. PTVE makes every effort to ensure product conformity at each manufacturing step while maintaining a safe production environment and a workforce superior for the thermoforming of food contact packaging products.
To ensure product safety, this position will:
· Adhere to PTVE’s GMP requirements.
· Identify product and/or situations that risk product contamination.
· Identify product and/or situations that violate cleaning and pest control requirements.
· Report equipment needing repair to supervision and avoid temporary repairs.
· Make sure that any recent maintenance work was cleaned up and does not pose any risk to product.
· Visually inspect raw materials for contamination.
· Inform quality regarding nonconforming product so it can be segregated.
· Make certain that no glass is brought into the facility.
· Not store product or production equipment directly on the floor.
· Only place goods in approved containers.
· Not use PTVE containers for storing miscellaneous items.
· Practice good hygiene and not eat, drink or use tobacco except in designated areas.
Work Relationship:
Work with: Production personnel
Reports to: Tech Manager
Supervises: Maintenance and Tooling personnel
Qualifications
Qualifications:
· BS in a technical or engineering field is preferred.
· In lieu of college degree, 8-10 years experience in maintenance environment is required.
· With a college degree, 5 years experience in a technical or manufacturing environment is required.
· 5-years experience in extrusion or thermoforming.
· 3-years supervisory, leadership and training experience.
· Strong sense of commitment and urgency.
· Strong problem solving and communication skills.
· Have strong project management skills.
· Must have working knowledge of MS Office Suite.
· Have ability to influence all levels of the organization
This job may require:
YES - Driving of cars, trucks, forklifts, or other equipment.
YES - Exposure to dust.
YES - Working at heights.
NO - Operation of foot controls or repetitive foot movement.
YES - Use of special visual or auditory protective equipment.
Job Locations US-NC-Greensboro
ID 2024-26518
Category Engineering
Position Type Full Time
Pay Type Salaried