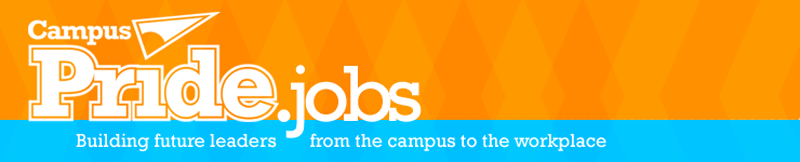
Job Information
WATTS Manufacturing Engineer III in Germantown, Wisconsin
We’re Watts. Together, we’re reimagining the future of water.
We feel proud every day about what we do. We're all part of the same crucial mission, no matter what function we support -- it's to provide safe, clean water for the world, and to protect our planet's most valuable resource.
What we do:
For 150 years, Watts has built best-in-class products that are trusted by customers in residential and commercial settings across the world. We are at the forefront of innovation, working with cutting-edge technology to provide smart and connected, sustainable water solutions for the future. Watts is a leading brand with a quality reputation — and we have a dynamic future ahead.
Bradley Corporation is a leader in commercial washrooms and safety solutions. Celebrating 100 years in business, we take pride in our work as a US manufacturer. With a culture focused on innovation, quality, and family, you will know your colleagues on a first-name basis in a friendly yet professional environment where your voice matters.
Summary
Responsible for designing, implementing, and improving manufacturing processes and systems used to create Bradley products that delight our customers. May direct work of others on projects and supervise manufacturing support workers and services as required.
Scope
This role has two focus areas which the employees in this role will be supporting, Advanced and Process. An employee in the ME role will focus specifically inside one of these two focus areas. The employee will likely have an overlap between roles and may be asked to complete tasks inside either focus area depending on business needs or as assigned by an Engineering Manager.
Advanced Manufacturing Engineering (AME):
Under the direction of the Advanced Manufacturing Engineering Manager, responsible for the research and development of manufacturing processes and equipment on new products and technology initiatives. Duties and Responsibilities:
· Lead the research, evaluation, and implementation of advanced manufacturing technologies to improve production efficiency, quality, and flexibility, ensuring that the latest trends and innovations are incorporated into manufacturing processes.
· Design, develop, and implement new manufacturing processes and systems for new product development, including equipment specification and selection, process development and optimization, and production planning, leveraging years of experience and expertise.
· Drive turn-key handoff of new production process to serial production, including product qualification and verification, process validation, and ramp-up planning, utilizing deep understanding of production and quality standards.
· Plan and execute large, complex multi-step capital equipment purchases, including vendor selection, specification development, budgeting, and project management, utilizing broad network of contacts and vendors.
· Conduct plant layout optimization to improve material flow, reduce waste, and increase productivity, leveraging years of experience and knowledge.
· Collaborate with cross-functional teams, including R&D, design, production, quality, and maintenance, to ensure that manufacturing processes are aligned with overall business objectives and customer needs, utilizing well-developed interpersonal skills and expertise in communication.
· Develop documentation related to new manufacturing processes, including work instructions, standard operating procedures, and process flow diagrams, with an emphasis on best practices, efficiency, and clarity.
· Ensure compliance with relevant regulations and standards, including environmental, health and safety regulations, and quality standards, with a keen awareness of changing regulations and trends.
· Mentor and train junior engineers on new processes and systems to ensure successful implementation and ongoing improvement, utilizing strong leadership skills and ability to coach and mentor effectively.
Process Manufacturing Engineering (PME):
Under the direction of the Continuous Improvement Manager, responsible for improving and sustaining manufacturing processes and equipment on existing products and improvement initiatives. May direct work of others on projects and supervise manufacturing support workers and services as required.
Duties and Responsibilities:
· Lead cross-functional teams to develop and implement complex process improvement initiatives that involve multiple departments or sites.
· Develop and implement strategic plans for manufacturing process improvements, capital investments, and overall site operations.
· Optimize existing manufacturing processes and systems to increase safety, quality, and efficiency.
· Drive implementation of Lean and Six Sigma methodologies, tools, and techniques to achieve process improvements and operational excellence.
· Mentor and train junior engineers on new processes and systems to ensure successful implementation and ongoing improvement, utilizing strong leadership skills and ability to coach and mentor effectively.
· Manage large-scale capital projects, including budgeting, procurement, installation, and start-up.
· Develop and maintain strong relationships with suppliers, contractors, and other external partners to ensure successful project delivery.
· Champion safety initiatives and ensure compliance with regulatory requirements.
· Conduct plant layout optimization to improve material flow, reduce waste, and increase productivity, leveraging years of experience and knowledge.
· Collaborate with cross-functional teams, including management, design, production, quality, and maintenance, to ensure that manufacturing processes are aligned with overall business objectives and customer needs, utilizing well-developed interpersonal skills and expertise in communication.
· Ensure that all manufacturing processes are documented, controlled, and executed in compliance with quality standards and regulatory requirements.
Education and Experience
· Bachelor’s degree in engineering or related discipline
· Five (5) to Eight (8) years relevant and progressive manufacturing engineering experience.
· Experience using office software products used in spreadsheets, documents, and presentations as well as with CAD software.
· Demonstrated ability to think deeply and critical of processes.
· Demonstrated Six Sigma problem solving project work.
· Demonstrated understanding and implementation of Lean fundamentals.
· Demonstrated Capital or large equipment implementation project work.
· Advanced: Demonstrated experience with new product development workflow and stage gates.
Competencies
Proficient use of office software products used in spreadsheets, documents, and presentations
Intermediate skills in AutoCad or other CAD software.
Exceptional written and verbal communication skills.
Works well in group problem solving situations.
Deal with a variety of concrete variables in situations where limited standardization exists.
Ability to write reports, business correspondence and procedure manuals. Must be able to read, analyze and interpret general business periodicals, professional journals, technical procedures or governmental regulations.
Identify and define problems, collect data, establish facts, and draw valid conclusions.
Ability to interpret a variety of instructions in written, oral, diagram or schedule form.
Physical Demands
The physical demands described here are representative of those that must be met by an employee to successfully perform the essential functions of this job. Reasonable accommodations may be made to enable individuals with disabilities to perform the essential functions.
While performing the duties of this job, the employee is regularly required to talk or hear. The employee is frequently required to use hands/ fingers to push, handle or feel, and reach with hands and arms. The employee is occasionally required to stand and walk. The employee must regularly lift and/or move up to 10 pounds, and occasionally lift and/or move up to 25 pounds. Specific vision abilities required by this job include close vision, color vision and depth perception. The noise level in the work environment is usually moderate.
Work Environment
The work environment characteristics described here are representative of those an employee encounters while performing the essential functions of this job. Reasonable accommodations may be made to enable individuals with disabilities to perform the essential functions.
Here’s why you’ll love working at Bradley:
Join a company where you'll meet passionate colleagues and partners from diverse backgrounds and experiences.
Enjoy a generous time off program with the option to purchase additional Paid Time Off. Benefit from twelve paid holidays a year, including a company-wide paid holiday shutdown between Christmas and New Year ’ s.
Benefit from work schedules that fully support your work/life balance.
Receive a competitive salary and a comprehensive benefits package, including medical, free basic dental, life insurance, and a 401(k) with company match, among other perks.
How we work:
At Watts, our culture is team-oriented and supportive. Employees here genuinely care about the quality of their work, and about each other. Our people are the heart of who we are and contribute to our longevity and continued success.
And this is a place where you can have a big career. No matter your role, there are opportunities for learning and development, and your daily contributions make a meaningful impact on the lives of people who use our products and on the future of water.
Watts is committed to equal employment opportunity. We follow a policy of administering all employment decisions and personnel actions without regard to race, color, religion, creed, sex, pregnancy, national origin, sexual orientation, age, physical or mental disability, genetic disposition or carrier status, marital status, military or veteran status, minorities, or any other category protected under applicable federal, state, or local law. Consistent with the obligations of state and federal law, Watts will make reasonable accommodations for qualified individuals with disabilities. Any employee who needs a reasonable accommodation should contact Human Resources.