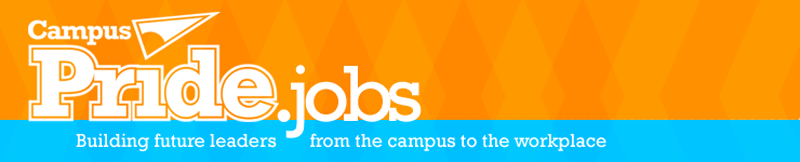
Job Information
Daisy Brand Manufacturing Systems Engineer-Packaging in Garland, Texas
Manufacturing Systems Engineer-Packaging
Job Details
Job Location
Garland - Garland, TX
Education Level
Bachelor's
Job Category
1530 - Engineers, all other
Description
The purpose of the Manufacturing Systems Engineer (Packaging) is to provide support in all aspects of the packaging systems. Provide focus and emphases on continuous improvement of manufacturing and packaging effectiveness along with reliability through the enhancement, development and complete documentation of sustainable processes, practices and support maintenance contained within the technical library. Supplement new technology and process implementation. Develop and/or enhance current operations and maintain technicians training. This role directly reports to the the Packaging Department Manager.
The Manufacturing Systems Engineer (Packaging) is responsible for ensuring each contractor/vendor working for him/her within a given department has been properly trained in all food safety, food quality and personal safety requirements including the pre-qualification programs. Although every supervisor and operator is responsible for a crucial part of the company's business, it is the Manufacturing Systems Engineer (Packaging) who is primarily responsible for leadership and integrity.
The Manufacturing Systems Engineer (Packaging) has the authority to take immediate corrective actions when dealing with Food Safety and Food Quality issues and is required to report these issues to the Plant Manager, Packaging Manger, Plant Engineering Manager and/or Quality Manager if further action is required. An assigned qualified employee will fill in for Manufacturing Systems Engineer in their absence.
Principal Duties:
Enhance Packaging Systems Effectiveness
Implement new packaging technology in addition to existing equipment.
Delivery of new lines/equipment - could include participation in the scope development all the way through the implementation, start up, and validation phases. The project origin could evolve from a multitude of sources, including business initiatives, quality improvements and productivity/cost-reduction activities.
Collaborate with Daisy Brand Production, Engineering, R&D and Quality Departments in order to effectively implement efficient packaging, sanitation, business and/or quality initiatives. Asses and enhance KPI and other target settings.
Leverage best practices for asset utilization, care and operation and capitalize on technologies with cross-functional and cross-plant teams. Enhancement or development of SOPs, TOS, PMs, Safety Procedures, etc., which requires personnel assessment and collaboration with the Packaging Manager(s), Maintenance Manager(s) or their designee, as well as the development of a sustainable auditing process.
Identify key process waste initiatives by seeking out opportunities to eliminate waste in all areas, from raw material and product delivery to the final packaging stage, including sanitation.
Perform, drive and document root cause analyses and corrective action investigations.
Track cost reductions in all process improvement activities, (i.e. equipment MRO spending, materials, utilities, yield, and labor) utilizing tools such as MRO and business financial tracking reports as well as equipment history CMMS reports compared against the expected budget.
Conduct pertinent operations record reviews. Assess deviations using statistical analysis and verify conformance to standards.
Assemble technical information for packaging systems. Review and audit the accuracy of process schematics, standard operating procedures, sanitation pin charts, line design rates (including line equipment design rate reviews) and upstream and downstream capabilities.
Training and Development
Assist plant leadership in learning the best implementation for new practices and technologies. Validate the learning plans and training needs of packaging and maintenance technicians associated with product and/or process improvements as well as new equipment commissioning.
Quality Control
Evaluate/determine potential impacts/risks to ideal cottage cheese and sour cream product body and texture that may arise from actual or proposed system change.
Define, document and communicate the scope of projector trials, sample collection processes, lead internal/external testing, assessment and isolation of required variables as well as the interpretation of results. Prepare and propose recommendations along with the sustainability plans necessary for successful fruition of a proposed change.
Document all projects, analyses, and audit-related work requests through the use of OneNote and other formal reporting means. Confer with management, production, and engineering staff to discuss project specifications and procedures.
Qualifications:
BS Science/Engineering packaging engineering, mechanical engineering, electrical engineering, industrial engineering, chemical engineering, or very closely related bachelors degrees. An emphasis in Packaging Science is preferred. Masters degree is a plus.
The Manufacturing Systems Engineer (Packaging) will have 2-7 years of related experience in a packaging engineering role within the food/dairy industry.
Project management experience desired.
Additional Education/Certifications (highly desired, but not required) - HACCP, USDA, FDA, OSHA, GMP, SPC, Green/Black Belt etc.
Skills:
Flexible/adaptable in various aspects i.e. work task priorities, work schedule depending on projects/tasks demand.
Experience with setting up and developing standards and SOP's in a manufacturing environment.
Passion and analytical aptitude as it relates to continuous improvement, statistics and process control.
Proven track record of working with teams and providing organizational influence and direction.
Excellent organizational skills, ability to prioritize multiple tasks and capabilities in multi-tasking.
Able to take initiative and work independently.
Able to balance multiple priorities.
Leadership skills.
Logical thought processes and problem solving expertise.
Results-oriented and highly focused on meeting (internal) customer expectations.
Exceptional interpersonal communication and presentation skills.
Excellent computer skills.
Experience:
Familiarity with dairy/food plant operations
Familiarity with cultured dairy products, procedures, and equipment
Lean Manufacturing/Six Sigma/Continuous Improvement. Root Cause, TPM, Kaizen, Autonomous Maintenance
Memberships in professional organizations
Other:
Strong work ethic, accountable, mature, and has management perspective.
Excitement for their role or field of endeavor.
Sets and enforces high standards.
Strong sense of right and wrong along with an understanding of corporate accountability.
Team player, readily offers other departments help when necessary.
Approachable, respectful, open and talkative.
Places the personal needs of others above their own self-ambition or corporate ambitions.
Detail oriented, precise, communicates with clarity. Tailors response to askers knowledge.
Enjoys speaking in front of small groups.
Good personal organizational skills and habits.
Patient but proactive. When prepared, not afraid to speak up in a group.
Company Overview
For five generations spanning over a century, Daisy Brand has been a family-owned company committed to providing the freshest, most wholesome dairy products. The company is headquartered in Dallas, Texas with manufacturing facilities in Garland, Texas (1998), Casa Grande, Arizona (2008), and Wooster, Ohio (2015).
Daisy is the market leader in two billion-dollar categories, sour cream and cottage cheese, and generates over half a billion in revenues annually. Daisy Sour Cream represents 1 out of every 2 sour cream purchases in the United States and is the largest sour cream brand in food service, military, and club. It is recognized by consumers for A Dollop of Daisy, a tagline that put this once small brand on the map. Daisy Cottage Cheese is America’s #1 cottage cheese brand and continues to bring new consumers into the category with its innovative single serve packaging and consistent high quality. Daisy recently expanded into a new category with the launch of two dip products and is in the process of expanding distribution.
Daisy's core values, Clean and Trust, resonate in all aspects of our business operations. In 2008, the Foundation for Financial Service Professionals awarded Daisy the prestigious American Business Ethics award.
While maintaining a strong culture of curious and innovative problem-solvers, Daisy Brand has more than doubled employment over the last 15 years and is continuing to grow. Currently, we are proud to employ over 650 full-time staff across more than 25 states throughout the United States.
At Daisy Brand, we value longevity and aim to foster a working environment where employees can envision a long-term career. Companywide, the average employee tenure stands at over seven years. Our corporate office and sales team each boast an average tenure exceeding eleven years, while our manufacturing facilities also demonstrate strong employee retention with tenures averaging over seven years.
Daisy Brand offers an industry leading benefits package that includes:
A no-deductible, $0 premium option for employee-only health coverage.
401(k) with 50% company match on first 8% of earnings you contribute.
Safe harbor and profit-sharing company contributions to 401(k).
Company paid short- and long-term disability coverage.
Company paid 2X annual salary life and AD&D insurance.
4 weeks annual paid time off.
Extra time off for volunteering.
Tuition reimbursement.
Fitness membership reimbursement.
And more
Daisy Brand is a nicotine-free company. Daisy Brand is an Equal Opportunity Employer. Veterans and disabled encouraged to apply.