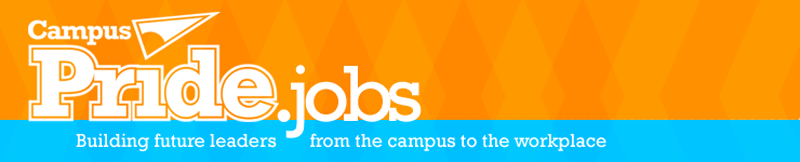
Job Information
LiDestri Maintenance Supervisor - 12-hour nights (6:00pm - 6:30am) in Fairport, New York
About LiDestri Food and Drink
LiDestri Food and Drink has grown from our roots as a pasta sauce and salsa manufacturer to become an R&D engine, formulating and producing innovative food products for our national and retailer brand partners. A family-run company based in Rochester, NY, LiDestri employs over 1,000 people across three U.S. locations. We have decades-long partnerships with some of the most respected consumer packaged goods (CPG) companies and the most highly inventive retailer brands.
Excellent Pay and Benefits:
Great career-pathing
Professional development, including unlimited online training courses
Health insurance with premium contributions
Dental, vision, HSA
100% company paid life insurance and long-term disability
401k – with employer match
Paid time off to include- vacation, sick pay, wellness time off, and 10 holidays
Company bonuses
And many more….
POSITION SUMMARY:
Provide both the mechanical and electrical expertise towards the processing, packaging and automatic warehousing operations as required, in an effort to be consistently improving the Overall Equipment Effectiveness
DUTIES & RESPONSIBILITIES:
Organize and manage maintenance staff to support the shift production in a seven day per week operation;
Crossover with both previous Maintenance Shift Manager and Production Supervisors for shift direction;
Communicate with Production Supervisors to ensure that all equipment and facility emergency problems are addressed;
Audit and train maintenance employees to procedures and best practice methodologies, as required.
Align team to prepare all set-up parts in conjunction with schedule needs;
Work with the Production Staff to insure all set-ups are correct, to include running water jars through the system for confirmation;
Conduct and lead LOTO, Confined Space and Hot Work Permit training and efforts;
Communicate all equipment cleaning efforts with the Sanitation Teams;
Point person on all emergency repairs and new request items;
Assist in the implementation of preventive maintenance activities;
Address all site alarms to insure both optimal equipment performance and continued personnel safety;
Participate and lead all maintenance shift activities involving the testing required during product development phases;
Communicate daily with Maintenance Scheduler to align workforce with preventive and routine maintenance workload;
Comply with site mechanical and electrical standards to improve production OEE and utility reliability;
Utilize CMMS to optimize asset utilization through scheduled preventive maintenance throughout asset useful life;
Assist in the utility cost reduction efforts;
Collaborate with Project Engineering to assist with the design and installation efforts;
Remain current with latest technology related to the manufacture of products;
Remain current with latest and emerging industry regulations and codes relative to mechanical and electrical systems design and operation;
Propose and implement improvement plans to enrich the Shift Maintenance Teams awareness around safety, quality and applied technology;
Coach, mentor and develop staff, including preparing and conducting employee performance appraisal;
Maintain employee work schedules including timecard approval, work assignments, job rotation, training, vacations and paid time off;
Report food safety & quality problems to personnel with authority to initiate action.
REQUIRED EDUCATION, SKILLS & EXPERIENCE:
AAS or Bachelor of Science in Mechanical/Electrical Engineering;
2 to 5 years’ experience leading a Maintenance Team supporting a 24/7 continuous manufacturing operation;
5 years’ experience in food, beverage or pharmaceutical industry and/or high speed packaged consumer goods manufacturing environment;
Effective communication skills:
Facilitator
Documentation
Collaborative work style
Proficient in Computerized Maintenance Management System software along with Microsoft Word, Excel, PowerPoint, Project;
Passion for continuous improvement, self-motivated and the ability motivate and influence others;
Lean manufacturing and/or Lean Six Sigma experience;
Certified Plant Maintenance Professional;
Lean Six Sigma Certification.
WORKING CONDITIONS:
Ability to work in a manufacturing environment with exposure to:
Long periods of standing/moving, working around moving mechanical parts/conveyors
Loud environment, hot/cold, wet/dry conditions
Lifting/carrying <50 pounds
Frequent reaching/pulling/climbing stairs/stooping/kneeling/bending
DISCLAIMER: The duties listed above are intended only as illustrations of the various types of work that may be performed and is not an inclusive summary of job duties and responsibilities. The omission of specific statements of duties or responsibilities does not exclude them from the position. This job description does not constitute an employment agreement between the employer and the employee and is subject to change by the Company as the needs of the Company and requirements of the job change.
#IND