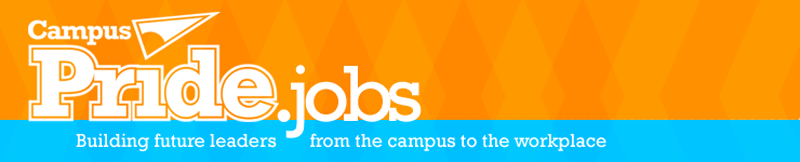
Job Information
Allied Mineral Products Sr. Manufacturing Engineer, Global Best Practices in Columbus, Ohio
Sr. Manufacturing Engineer, Global Best Practices
Location/Region: Columbus, Ohio
Work Style: On-Site
Travel: 15-25%
Allied Mineral Products
We are not looking for employees, we are looking for owners! We are proud to be an employee owned ESOP company where every employee has a vested interest in the success of the organization. As an ESOP company, Allied currently contributes 25% of annual earnings (base pay and profit sharing) to your individual employee retirement account each year.
Since our founding in 1961, Allied Mineral Products has grown into a leading global producer of monolithic refractory ceramics. Our sales, research, engineering, and manufacturing teams provide unmatched customer service and deliver quality engineered ceramic solutions to every furnace and industrial application.
Allied is powered by talented employees who work in a productive, strategic, and collaborative culture. The Allied Way has a lot of meaning, and a lot of history. Above all, we are dedicated to “being there worldwide with advanced ceramic and engineered solutions.”
Allied has over 1,100 employees worldwide serving multiple industries in more than 100 countries.
We are seeking highly motivated individuals with diverse backgrounds, experiences, continuous improvement values, and a strong work ethic.
If your goals and values align with Allied’s, we want you to join our team.
About this Position:
We are seeking a Sr. Manufacturing Engineer who will identify, document, standardize, and continuously improve best practices across our global manufacturing operations. Focus areas include safety, quality, and efficiency of Allied’s monolithic and shapes manufacturing processes, equipment, and procedures. The ideal candidate possesses a strong background in manufacturing and engineering with a keen understanding of diverse industrial practices and a proven ability to drive global process optimization initiatives.
Key Responsibilities: This role requires a combination of strong analytical knowledge, project management experience, manufacturing strategy development, and effective communication skills. Key pillars for this position include:
Global Best Practices Strategy
Develop and implement a comprehensive strategy for identifying, evaluating, and adopting best practices across all global manufacturing sites.
Collaborate with regional teams to ensure cultural and operational nuances are considered in the implementation of global best practices.
Cross-Cultural Collaboration:
Work closely with manufacturing teams at all global manufacturing plants to understand local practices and challenges.
Facilitate cross-cultural collaboration to foster a unified approach to global best practices implementation.
Coordinate and facilitate regularly scheduled, virtual and in-person group meetings to enable the sharing of information.
Standardization and Documentation:
Observe and benchmark all Allied’s monolithic manufacturing systems and processes.
Establish global standards for these systems and manufacturing processes, ensuring consistency in quality, efficiency, and safety.
Create detailed documentation and training materials to support the adoption of standardized best practices.
Continuous Improvement:
Drive a culture of continuous improvement on a global scale, encouraging teams to proactively identify and implement opportunities for optimization.
Monitor and evaluate the effectiveness of implemented best practices, making adjustments as needed.
Technology Integration:
Explore, recommend, and support the integration of advanced technologies and Industry 4.0 solutions to enhance global manufacturing efficiency.
Collaborate with technology teams to ensure seamless integration and scalability.
Develop and deliver global training programs to educate manufacturing teams on new best practices and process improvements.
Foster a global mindset by promoting knowledge-sharing and collaboration across regions.
Qualifications, Experience, and Skills:
Bachelor of Science degree in Mechanical Engineering, or other similar technical field, or equivalent work experience.
At least five years of related work experience preferred.
Requires strong experience in manufacturing engineering and process optimization.
Strong knowledge of industry best practices and emerging trends in manufacturing.
Proficiency in data analysis tools and experience in implementing data-driven decision-making processes.
Excellent communication and interpersonal skills.
Ability to work collaboratively in a cross-functional team environment.
Project management skills with a focus on meeting deadlines and achieving project goals.
Total Rewards:
Competitive base pay
As an ESOP company, Allied currently contributes 25% of annual earnings (base pay and profit sharing) to your individual employee retirement account each year
Paid time off including, vacation, holidays, and sick time
Medical, Prescription Drug, Dental, and Vision programs
401K program
Life, Short-Term, and Long-Term disability
Flexible work schedules
Career Growth:
Growth and advancement opportunities
Education reimbursement for continued learning
Allied Mineral Products Holding, Inc. is an Equal Opportunity Employer/Veterans/Disabled.
Sr.