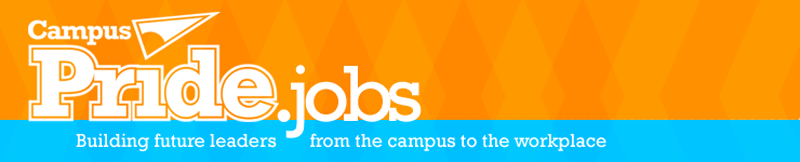
Job Information
FUJIFILM DIOSYNTH BIOTECHNOLOGIES Facilities Maintenance Technician III in College Station, Texas
Overview 2 Maintenance Technicians 6am-6pm and 6pm-6am shift
The work we do at FDB has never been more importantand we are looking for talented candidates to join us. We are growing our locations, our capabilities, and our teams, and looking for passionate, mission-driven people like you who want to make a real difference in peoples lives. Join FDB and help create the next vaccine, cure, or gene therapy in partnership with some of the most innovative biopharma companies across the globe. We are proud to cultivate a culture that will fuel your passion, energy, and drive - what FDB call Genki.
College Station, Texas may be a small, university town, but the lively cultural scene and local amenities make it a great place for families as well as those who want the ease of small-town life and the convenience of living close to the vibrant pulse of big cities. Eighty-seven percent of Texas' population lives within a 180-mile radius, so we are in the center of it all in Texas. And our site is nestled in the hub of innovation, representing a source of pride for the area.
Summary: The Maintenance Technician III, under the supervision of the Facilities Maintenance Supervisor, or designated supervisor will be responsible for performing various aspects of utilities, facilities and process equipment maintenance, utilities operation and support for the Texas Biological Facility (TBF), the Flexible Biological Facility (FBF) and the National Center for Therapeutic Manufacturing (NCTM) on behalf of Fujifilm Diosynth Biotechnology Texas (FDBT).
Primary responsibilities include various aspects of maintenance, utilities operation and support for facilities, utility equipment and biotech processing equipment.
This position will be required to use technical manuals, on-line resources and OEM representatives to maintain the equipment operational with a minimum of downtime. Strict adherence to Standard Operating Procedures (SOPs), cGMPs and Quality Standards in a Pharmaceutical Manufacturing facility are mandatory.
External US
Essential Functions:
- Provide maintenance, reliability and operational support for clean utility equipment, including clean utilities such as clean gases, steam generated Water for Injection (USP), clean steam systems, and RODI water systems.
- Provide maintenance, reliability and operational support for plant utility equipment, including utilities such as air compressors, air dryers, steam boilers, chillers, heating hot water boilers, HVAC systems and waste disposal systems.
- Provide maintenance, reliability and operational support for fermenters, bioreactors, tanks, chromatography columns, filtration skids, centrifuges, autoclaves, agitators, etc. in coordination with manufacturing operators or supporting departments.
- Provide maintenance and operational support for facilities, building maintenance and grounds.
- Technician will be responsible for critical environment controls, maintenance on critical laboratory equipment within GMP clean rooms and environmental controlled areas.
- Able to perform troubleshooting or reliability tasks on temperature controlled process equipment such as refrigerators, freezers, ultra-low temperature freezers and cold rooms.
- Ensure compliance, as set forth in internal quality protocols and SOPs including cGMP and FDA regulatory guidelines.
- Able to perform routine work orders and maintenance functions with little supervision after training and work in support of technicians or specialized maintenance contractors or OEM on more complex equipment interventions.
- Able to work with other contractors, engineers, validations and quality control personnel regarding changes or improvements to the systems.
- Be able to write or assist with SOPs, JHAs, HECPs and preventive maintenance procedures for utilities equipment.
- Maintain all mandatory training requirements current, ensuring compliance to site procedures and job erformance qualifications.
- Demonstrate continuous personal pursuit to increasing job knowledge and proficiency with different systems.
- Maintain a positive, professional, and customer-oriented attitude.
- All other duties as may be assigned.
Required Skills and Abilities:
- Strong mechanical, electrical and instrumentation knowledge of equipment, using PandIDs, equipment manuals, specifications, SOPs, and be able to use proper judgment when taking corrective actions during equipment malfunctions.
- Strong technical troubleshooting / problem solving skills. Possess or have the ability to gain knowledge with respect to the operation and maintenance
- Knowledge of a wide variety of typical maintenance tasks, including PM, troubleshooting systemic problems such as pneumatic, mechanical, electrical, electronic and ladder logic programming. General principles of engineering, operations and maintaining process equipment and the tools and equipment required to perform many of the daily maintenance tasks.
- Knowledge of bio-medical, bio-technical equipment, both upstream and downstream highly desirable.
- Able to develop clear and correct maintenance procedures for technical/process equipment using the OEM manual and some system knowledge.
- Possess or have the ability to gain knowledge of NFPA 70E requirements for safe work practices.
- Possess or have the ability to gain knowledge of FDA, OSHA, EHandS, EPA, and state of Texas requirements.
- Strong written and verbal communications skills, be self-motivated and possess interpersonal skills.
- Ability to learn quickly and work effectively with little supervision when needed.
- Desire to work in a fast paced, state of the art, alternately research and customized manufacturing facility.
- Working knowledge of MS Office products (Word, Excel, Outlook, and PowerPoint) as well as use of Computerized Maintenance Management System, CMMS.
- Knowledge of cGMP and cGDP requirements and procedures predisposed to documentation of work performed, documenting non-conformance conditions and maintaining clean work areas.
Working Conditions and Physical Requirements:
The physical demands described here are representative of those that must be met by an employee to successfully perform the essential functions of this job. Reasonable accommodations may be made to enable individuals with disabilities to perform the essential functions. While performing the duties of this job, the employee is regularly required to:
- Experience prolonged sitting, standing, walking, bending, stooping and stretching.
- Use hand-eye coordination and manual dexterity sufficient to operate portable tools, test instruments, as well as a computer keyboard, telephone, calculator, and other office equipment is required.
- Have a normal range of vision.
- The ability to regularly lift and/or move up to 50 pounds.
- Climb ladders and stairs of various heights.
- Be exposed to wet or humid conditions.
- Be exposed to outdoor weather conditions.
- Be exposed to noisy environments.
- Attendance is mandatory.
- This position will be on-call for maintenance issues in rotation with other technicians.
- This position may require coverage of different shifts, weekends and holidays.
Minimum Qualifications:
High School Diploma or GED with six (6) years of relevant maintenance work experience, preferably in a bio-pharma facility in a bio-pharma facility with the above listed equipment; OR
Associates Degree, Technical Degree or Certificate in Mechanica