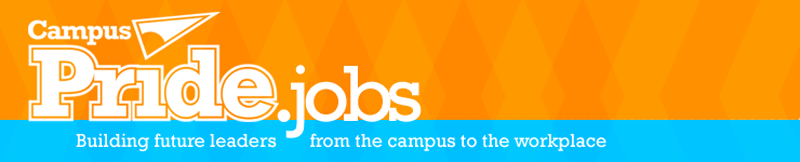
Job Information
Watco Companies L.L.C. Maintenance Shop Supervisor in (Cahokia), United States
Start a Watco Career and Discover the Difference
Keep the world’s supply chain moving. That’s what the Watco team does every day at our short line railroads, switching sites, terminals, ports, and logistics hubs.
Whether you’re at one of these locations or in a support-services role, there’s one thread that ties everyone together. We’re all on the same team. One Watco (https://www.youtube.com/watch?v=yZUdmGlPP8c) .
Here’s what you can expect from Watco:
Award-winning culture recognized by Forbes and Newsweek
Competitive compensation and benefits (https://www.watco.com/benefits/)
Paid on-the-job training with peer trainers
Operations training at the Safe Performance Center (https://vimeo.com/895928733) in Birmingham, Alabama
Leadership and development programs offered through Watco University
Career advancement opportunities
POSITION OVERVIEW:
The Maintenance Shop Supervisor is responsible for overseeing daily maintenance activities within the shop, ensuring high-quality work, and managing a team of mechanics, technicians, and support staff to meet operational goals. This role combines leadership with hands-on technical expertise to maintain, repair, and troubleshoot machinery and equipment. As a senior technical expert, the Maintenance Shop Supervisor provides guidance and training to staff while ensuring adherence to safety and compliance standards. The Supervisor is also involved in performance evaluations, scheduling, and continuous improvement initiatives to enhance overall equipment reliability and shop efficiency.
ESSENTIAL DUTIES AND RESPONSIBILITIES :
Supervise and schedule mechanics and technicians, assign tasks based on skill level, job priority level and equipment needs, and ensure all maintenance work meets safety, quality, and operational standards.
Act as a liaison between management, planning teams, and maintenance staff to align goals and address challenges.
Provide performance feedback, mentorship, and training to promote skill development and maintain a positive work environment.
Perform advanced troubleshooting, repairs, and routine inspections on machinery, equipment, and systems (mechanical, hydraulic, electrical, and pneumatic) to ensure optimal performance of equipment while providing opportunities to enhance culture of training and collaboration.
Ensure all maintenance activities comply with company and regulatory safety protocols, including OSHA and EPA standards, while collaborating with QA/QC inspectors to verify work quality and compliance.
Maintain accurate documentation of maintenance activities, repairs, inspections, and parts inventory.
Coordinate with the Parts Coordinator to ensure parts availability
Oversee ordering, usage, and inventory tracking, and manage cost control by optimizing resource use and minimizing waste.
Provide regular reports to the Maintenance Manager on maintenance activities, equipment status, and team performance, while maintaining accurate records in the maintenance management system.
Assist in planning and scheduling major equipment overhauls or shutdowns
Identify opportunities to improve maintenance processes, reduce downtime, and enhance equipment reliability
Participate in safety and training programs to ensure team compliance and recommending necessary improvements to protocols or equipment
KNOWLEDGE, SKILLS & ABILITIES:
Advanced troubleshooting and mechanical knowledge across a variety of systems (mechanical, hydraulic, pneumatic, and electrical).
Understanding of safety, compliance, and regulatory requirements (OSHA, EPA).
Strong leadership, team-building abilities, and organization skills.
Proficiency with maintenance management software and basic computer skills.
Ability to manage and prioritize maintenance tasks in a fast-paced, dynamic environment.
Capacity to work independently and as part of a team to achieve maintenance goals.
Ability to identify and implement process improvements to enhance shop efficiency and equipment reliability.
QUALIFICATIONS:
Minimum of 8 years of experience in maintenance and repair of industrial equipment, with at least 3 years in a supervisory or foreman role.
Strong background in heavy equipment, diesel engines, hydraulic, and pneumatic system.
High school diploma or equivalent; technical certifications or a degree in a related field is preferred.
Certifications in welding, hydraulics, or diesel mechanics are a plus.
WORK ENVIRONMENT & REQUIREMENTS:
This role is performed in a railroad setting in locations such as a short line railroad, switching sites, terminals, ports, and logistics hubs. This role requires the ability to work safely and effectively in this type of setting and role requires mobility and manual dexterity to navigate an industrial environment, including the use of standard office equipment. Candidates must be able to communicate effectively in person and via radio or phone and have the vision to read various materials and inspect safety signs. Physical tasks include lifting to 50 pounds, using ladders and power tools, and performing fieldwork in various weather conditions while being exposed to noise, dust, and machinery. This role requires the ability to perform the essential job functions consistently, safely, and successfully in accordance with the ADA, FMLA and other federal, state, and local standards, including meeting qualitative and/or quantitative productivity standards along with the ability to maintain regular, punctual attendance in accordance with the ADA, FMLA and other federal, state, and local standards.