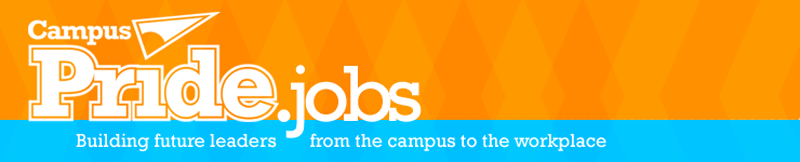
Job Information
WATTS Maintenance & Engineering Technician in Avondale, New Zealand
POSITION SUMMARY
The Maintenance & Engineering Technician is responsible for producing, modifying, repairing and maintaining high-quality tools, dies, jigs, moulding dies, press tooling, machinery and fixtures to support production processes in line with ISO and Company standards, with a strong focus on quality and safety.
PRINCIPAL RESPONSIBILITIES AND DUTIES
Maintenance & Engineering
Setting and operating production machinery.
Read and interpret technical drawings, specifications and CAD models.
Design, fabricate, assemble and maintain tools, dies, jigs, and fixtures used in the manufacturing process to ensure proper fit and functionality.
Repair and maintain plastic injection moulding dies.
Collaborate with R&D Engineers and production teams to develop innovative solutions.
Assist in the design and manufacture of automation equipment.
Perform routine maintenance and troubleshooting on equipment to ensure optimal performance.
General fitting, machining, welding and fabrication.
Conduct regular inspections and preventive maintenance on production machinery to minimise downtime.
Diagnose and repair mechanical issues, ensuring machinery operates efficiently and safely.
Collaborate with colleagues to streamline operations and improve equipment reliability.
Process and Quality Control
Ensure all work complies with safety and quality standards.
Contribute to quality control improvements and checks.
Adhere to ISO manual procedures and ensure any discrepancies are brought to the attention of the Machine Shop Supervisor and/or Plant manager or Senior Manager R&D ANZ (as appropriate).
Follow production schedule.
Contribute to the implementation of any plant automation and efficiency improvements or general site improvements.
Regulatory and Compliance
Comply with relevant legislation, regulations and policy that impact on/relate to Apex.
Keep sensitive customer and/or product information confidential in accordance with applicable legislation and Watts policies.
Health and Safety
Maintain a clean and safe working environment, adhering to all health and safety regulations.
Compliance with all Apex Health and Safety policies and procedures.
Actively contribute to Health and Safety initiatives and the continuous improvement of all aspects of Health and Safety.
Report incidents, near misses and safety opportunities in a timely manner and in contribution to company targets.
Ensure your actions follow safe work practices to maintain a safe environment for yourself and everyone on site.
Other Responsibilities
Ensure individual work area complies with 5S.
Share technical support and expertise in continuous improvement initiatives.
Identify opportunities for waste reduction, safety and efficiency improvements through quick Kaizen submissions.
EDUCATION
Bachelor or Diploma in Mechanical Engineering, Toolmaking, or a related field.
Current Forklift Licence preferred (training available if not held)
EXPERIENCE
- Previous experience in toolmaking, fitting, and turning within a manufacturing environment.
MINIMUM REQUIRED SKILLS
Effective communication skills – written and verbal.
Ability to work independently as well as collaboratively in a cross-functional team environment.
A focus on quality and continuous improvement.
Proficient in reading and interpreting technical drawings, specifications, tolerances and CAD designs.
Strong knowledge of machining processes, experienced in manual turning milling and grinding operations (CNC machining experience beneficial).
Experience in accurately using measurement equipment to ensure components are produced within specification e.g. vernier calipers, micrometers and gauges.
Welding and fabrication skills.
Ability to select appropriate materials and cutting tools to achieve desired specifications.
Excellent manual dexterity and attention to detail.
Ability to manage workload independently and prioritise tasks effectively.
Familiarity with lean manufacturing principles and continuous improvement methodologies.
Basic computer skills using Microsoft Office.
Willingness to work flexible hours, including overtime if necessary.
Valid New Zealand driver’s license.
PHYSICAL REQUIREMENTS
Physical ability to lift heavy materials and stand for extended periods.
Permission to complete a pre-employment heath check to ensure meets standard required for role.
WORK ENVIRONMENT
Machine Shop.
Flexibility to support other production areas as required by operational workloads.