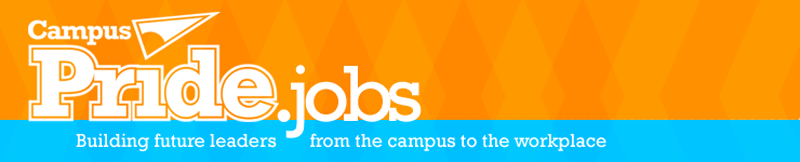
Job Information
Integra LifeSciences Manufacturing Engineer II in Anasco, Puerto Rico
Changing lives. Building Careers.
Joining us is a chance to do important work that creates change and shapes the future of healthcare. Thinking differently is what we do best. To us, change equals opportunity. Every day, our colleagues are challenging what's possible and making headway to innovate new treatment pathways to advance patient outcomes and set new standards of care.
ESSENTIAL DUTIES AND RESPONSIBILITIES
To perform this job successfully, an individual must be able to perform each essential duty satisfactorily.
1.Development and update of manufacturing process flow chart.
2.Maintenance and update of manufacturing documentation such as: BOM/production routers, procedures, drawings, specifications, etc.
3.Maintenance and upgrade existing products/processes.
4.Develops and/or executes validations of revised/new raw materials, products, processes and/or equipment following Integra procedures.
5.Develops, coordinates, and implements the change controls related to each manufacturing engineering project. Evaluates and assures completeness of change control requirements for projects under responsibility.
6.Develops the required documentation, procedures, drawings, protocols, engineering change notices, technical reports and other information as required by the company.
7.Submits requisitions of components, materials, equipment, machinery, services, tooling and fixtures to supervisor for approval as part of engineering projects.
8.Oversee installations to ensure machines and equipment are installed and functioning according to specifications. Troubleshoots equipment/processes that do not perform as intended.
9.Provides engineering technical support to manufacturing areas.
10.Develops and implements scrap reduction initiatives.
11.Develops and implements capacity increase projects.
12.Evaluates and update manufacturing time standards.
13.Develops and implements cost improvement projects.
14.Analyzes layout of equipment, workflow, assembly methods, and work force utilization standards to maximize the manufacturing processes efficiency.
15.Evaluates and implements product labeling and printed materials changes.
16.Evaluates and implements raw material/components changes.
17.Evaluates and/or implements change controls and engineering change orders (ECO, DCO, MCO).
18.Evaluates, investigates and documents non-conformances incidents. Provides support on the assessment and disposition of non-conforming material.
19.Completes assigned Non-Conformance and CAPA investigations and prepare investigation reports.
20.Implementation of corrective and preventive actions for process related concerns.
21.Supports in the investigation and resolution of supplier quality issues.
22.Supports the introduction of new businesses and products/processes.
23.Participates in the development of the new processes, process transfers and continuous improvement, and issue resolution.
24.Supports the transfer of products/processes to outside facilities.
25.Development of process controls for new and existing equipment and/or processes.
26.Reviews and approves validations and completion reports for new and existing products, processes and equipment.
27.Develops and implements metrics to monitor the performance of manufacturing areas.
28.Develops and implements Six Sigma/Lean projects and quality improvement plans. Identify and implement opportunities for continuous improvement.
29.Develops and conducts product/process training programs and demonstrates skills to trainees, using hand tools, precision measuring instruments, following schematics, drawings, procedures, and manufacturer's specifications.
30.Prepares information for Quality Management Reviews and Operational Reviews such as: trending charts, Pareto analysis, etc.
31.Participates in the compilation and review of technical documentation for both domestic and international regulatory submissions.
32.Participates in external audits such as: FDA, Notified Body (BSI) and Corporate, among others.
33.Will partner with Manufacturing and Quality departments to ensure that the development, manufacture and distribution of medical products is in compliance with corporate policies and regulatory requirements (International Organization for Standardization (ISO)/ European Norm (EN)/ European Medical Device Directive (MDD)/ Canadian Medical Device Regulation (CMDR) standards/ sections, Quality System Regulation (21CFR 820, 21CFR 11 and other associated FDA regulations), and other applicable regulatory agencies).
34.Performs other related duties as necessary.
DESIRED MINIMUM QUALIFICATIONS - Education and Experience
The requirements listed below are representative of the knowledge, skill, and/or ability required for this position.
*BS in Engineering, preferably Mechanical, Industrial, Electrical, Chemical, or Biomedical.
*Master's degree is a plus.
*PE License strongly desired.
*Lean/Six Sigma Green or Black Belt Certification is a plus.
*Minimum of 3 - 5 years of experience in the medical device and/or pharmaceutical manufacturing environment; with at least three (3) years in a manufacturing process or quality engineering position and preferably with exposure to Design Control and Product/Process Transfer.
*Knowledge in Collagen and Silicone technologies and materials as well as lyophilization and dispersion preparation is highly desirable.
*Knowledge of FDA, OSHA, EPA, and GMP's and ISO requirements.
*Knowledge in Organizational Excellence and Lean/Six Sigma.
*Strong Project Management skills.
*Effective knowledge in Microsoft Project software.
*Knowledge of cost control, and development of guidelines, training, and maintenance programs.
*Ability to lead teams through complex projects and provide departmental technical leadership.
*Must have excellent communication skills and a strong track record of working cross-functionally.
*Must have demonstrated ability to think strategically.
*Able to develop technical documentation such as: Change Controls, Validation Plans, Validation Protocols, Technical / investigation reports, SOP, and others.
*Experience in Design Control procedures and regulation is desirable.
*Teamwork oriented and self-starter.
*Fully bilingual (English and Spanish).
*Availability to work extended hours in the day and weekends as required.
Integra LifeSciences is an equal opportunity employer, and is committed to providing equal employment opportunities to all qualified applicants and employees regardless of race, marital status, color, religion, sex, age, national origin, sexual orientation, physical or mental disability, or protected veteran status.
This site is governed solely by applicable U.S. laws and governmental regulations. If you'd like more information on your rights under the law, please see the following notices:
EEO Is the Law (https://www.eeoc.gov/laws/index.cfm) | EOE including Disability/Protected Veterans (https://www.eeoc.gov/eeoc/publications/ada_veterans_employers.cfm)
Integra LifeSciences is committed to provide qualified applicants and employees who are disabled veterans or individuals with disabilities with needed reasonable accommodations in accordance with the ADA (https://www.eeoc.gov/eeoc/publications/fs-ada.cfm) . If you have difficulty using our online system due to a disability and need an accommodation, please email us at careers@integralife.com or call us at 855-936-2666.
Integra - Employer Branding from Integra LifeSciences on Vimeo (https://player.vimeo.com/video/265760526)