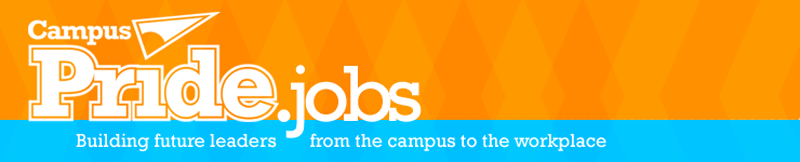
Job Information
M. C. Dean Electrical Crew Leader in Aldie, Virginia
Electrical Crew Leader
ID 13137
Location Aldie, VA
Apply Now (https://phg.tbe.taleo.net/phg04/ats/careers/v2/applyRequisition?org=MCDEAN&cws=62&rid=13137)
Planning, organizing and scheduling crews to complete assigned work orders, including assigning tasks, assuring the work is being installed in a high-quality manner and performing quality inspections. Monitors task completion, compliance and prevents safety issues.
Responsibilities include:
Productivity Planning for assigned scope of work.
Assuring his/her crew meets daily productivity benchmarks:
Material Phasing – Organize Material by specific areas/floors. (keep track of materials inventories).
Tools & Equipment - Identify all tools and equipment required to support each crew (Gang box Assignments, tool inspection and keep track of tools by signing sheet in-out).
Information Packages – Each crew activity must have information packages (contract drawings, shop drawings, panel schedules, cut sheets, etc…).
Keep control of breaks (loss time of personal breaks smoking time, conversation time).
Daily hour/unit reports for their crews – Submit hours/units daily for each employee assigned to Foreman on established from (Standard Time Sheet).
Quality control inspections of work completed – Must follow established QC plan & check lists.
Responsible for installing the work in a professional manner and high-quality standard.
Maintaining accurate as built drawings – As-built drawings are to be updated and logged onto master record contract drawings a minimum of once a week.
Inventory of all tools & equipment at the day’s end for assigned tools & equipment. (Everything must be accountable & secure). inventory/inspection sheets to be turned in every Monday.
Lost/Stolen/Damage tool report.
AHA’s – All AHA’s related to Foreman’s scope of work must be reviewed, signed by each crew member and stored at their gang box in the field.
Support Equipment Inspection – Foreman must submit daily equipment inspection sheets for all equipment assigned to Foreman once a week.
Accident/Incident Reporting & Investigation – Must follow the established procedures for responding and reporting accident and incidents. All reports must be submitted within 24 hours of accident/incident.
Clean Up – Foreman and Crew leader are responsible for all clean up related to their scope of work. All work areas are to be left in a broom swept condition at the end of the day.
Quality of work completed must follow:
Ensure installation meets/exceeds codes, contractual obligations, best practices and other requirements as mandated by the Corporate Quality Policy.
Ensure all facets of Project Quality Plan are reviewed and implemented. Any deviations are properly documented and communicated to site Q.C. representative for approval prior to
proceeding any further.
Participate and assist the Site Q.C. representative in the implementation of 3-Phase Quality Control, which includes Preparatory, Initial & Follow-up for each Definable Feature of Work (DFOW) under the crew leader’s responsibility.
Properly document and return the CQC checklists to Site Q.C. representative ensuring installation inspections are done timely and facilitate the adherence to QAQC schedule.
Initiate Various Discrepancy Notices (EDN, DDN, PDN, FDN, ADN, PITDN, CDN) in order to ensure issues arising during construction are properly documented and communicated for resolution.
Review and provide feedback on weekly installation quality scorecards as generated by QAQC service center to ensure systemic issues are addressed through formal root cause, corrective and preventive action.
Review ongoing quality issues identified in the daily Q.C. report with the crew to ensure mitigation/elimination of the nonconformities.
Ensure nonconformity tags identified on discrepant installation by site Q.C. representative is timely resolved.
Participate in QAQC Design Review of Engineering & Coordination drawings to identify constructability issues.
Participate and provide feedback on Quality portion of the daily ORM work briefing.
Education:
6+ years of experience in the electrical industry with a Highs School Degree or GED
4+ years of experience with an associate degree
Physical Abilities:
Lifts at least 100 pounds at one time and 60 pounds for an extended period of time.
Relocates a 12-foot stepladder without assistance.
Works at various heights up to 60 feet and can climb and maintain balance on scaffolds, aerial lifts, catwalks and all types of ladders.
Walks, climbs, lifts, squats, crawls, kneels, pushes, pulls and reaches overhead on a routine and repetitive basis.
Possess good vision (may be corrected vision), the ability to see in color, and the ability to hear and communicate in English.
May use a standard ladder without exceeding the weight limit while carrying tools.
Tell when something is wrong or is likely to go wrong. It does not involve solving the problem, only recognizing there is a problem.
Apply general rules to specific problems to produce answers that make sense.
Combine pieces of information to form general rules or conclusions (including finding a relationship among seemingly unrelated events).
See details at close range (within a few feet of the observer).
Listen to and understand information and ideas presented through spoken words and sentences.
Applicants for this position may be required to obtain or provide proof of flu shots or of other vaccinations depending on customer requirements and nature of the position or demonstrate a valid basis for exception.
EOE Minorities/Females/Protected Veterans/Disabled
VEVRAA Contractor